Making of a mountain trail bike
The suspension may be conceived on a computer screen but it’s born on the testing trails of Afan – we witness the labour pains of the Nukeproof Mega.
>>> Afan Forest, South Wales trail centre guide
Every autumn, British manufacturers using RockShox suspension meet SRAM technicians at a low-key tuning camp to perfect their latest machines. It’s a crucial final stage for a modern trail bike and we peeked behind the embargo curtain with Nukeproof last year to see exactly what goes down.

Afan’s abundance of varied trails make it the ideal shock-tuning location
Like most brands, Nukeproof works behind the scenes years in advance. Long before hitting the shops or the Internet, a team of designers, engineers and product managers brainstorm the original concept of any new bike. Everything from frame material and construction techniques, commercial potential, strength to weight ratios, geometry, suspension rates, specification and finish have to be considered; each informed by shed loads of influencing factors.
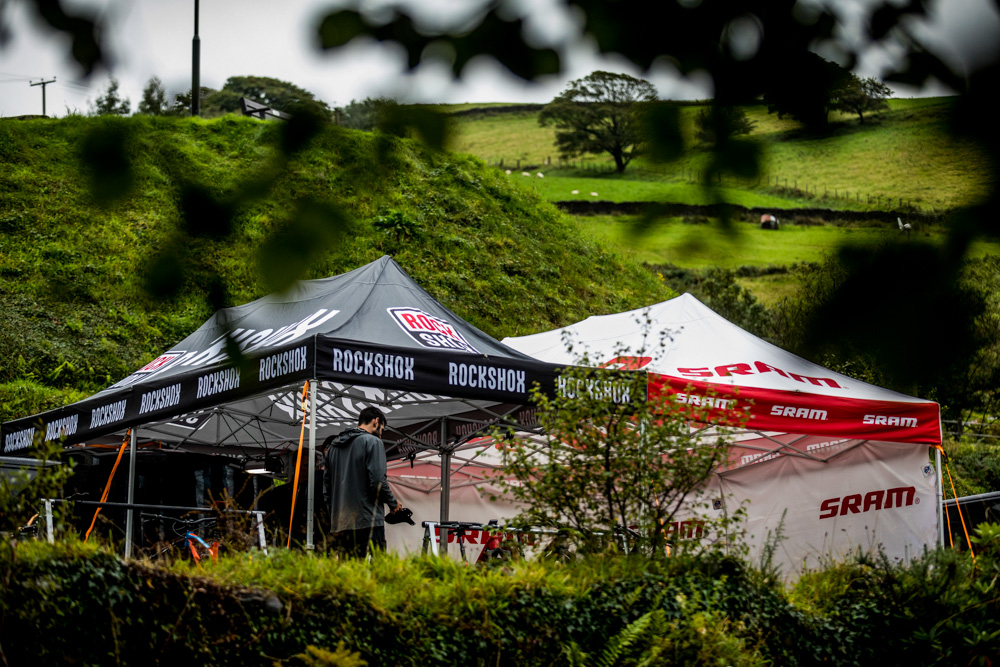
Base camp’s the place for quick tune-up
A bike’s specific remit is often defined in terms of suspension travel. For Nukeproof making its Mega, that meant roughly 160/170mm travel (the industry consensus for ‘enduro’), but any new bike faces ever-shifting constraints on top of this too. Things like manufacturing costs, new trends or design ideas, fresh technologies and standards, and even rider or race team feedback also figure in the equation.
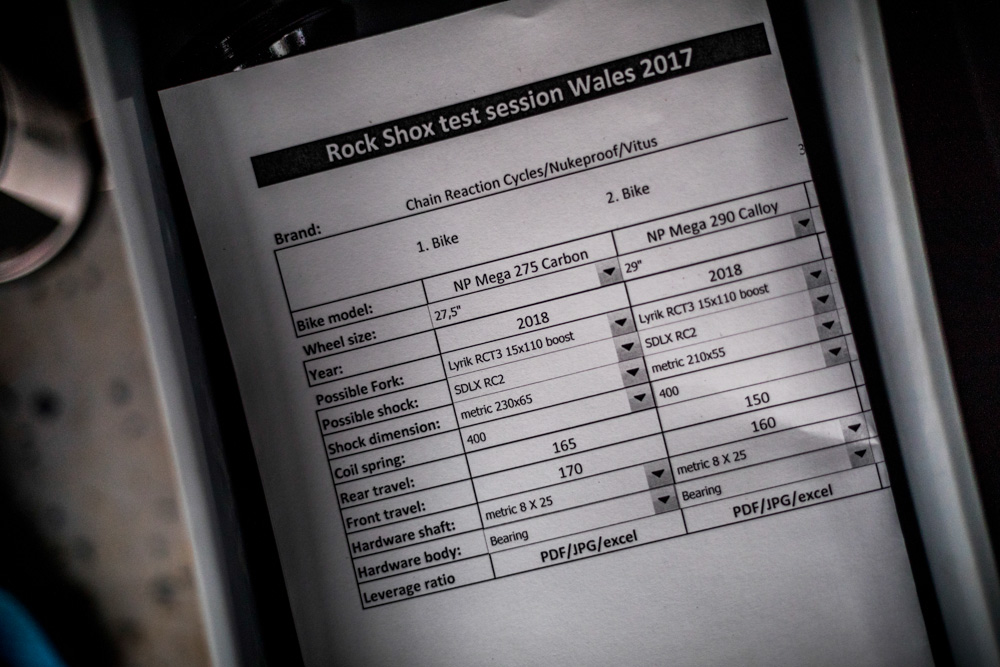
Testing notes record each shock’s configuration
Meeting up with RockShox each year is a bridge that connects computer modelling and paper drawings with real world testing scenarios. A new bike’s success can hinge on the quality of the suspension system, so tuning with the suspension manufacturer is critical.

Inside a suspension technician’s toolbox
Before any brands arrive to tune, suspension and component manufacturers like SRAM keep (more powerful) manufacturers in the loop about forthcoming technology to smooth forward planning and ensure loyal customers don’t get caught cold. It’s a lengthy development process, and customers buying a new bike now stand a good chance their latest toy was prototyped, refined and signed off years ago by designers and engineers now working as far ahead as 2021.
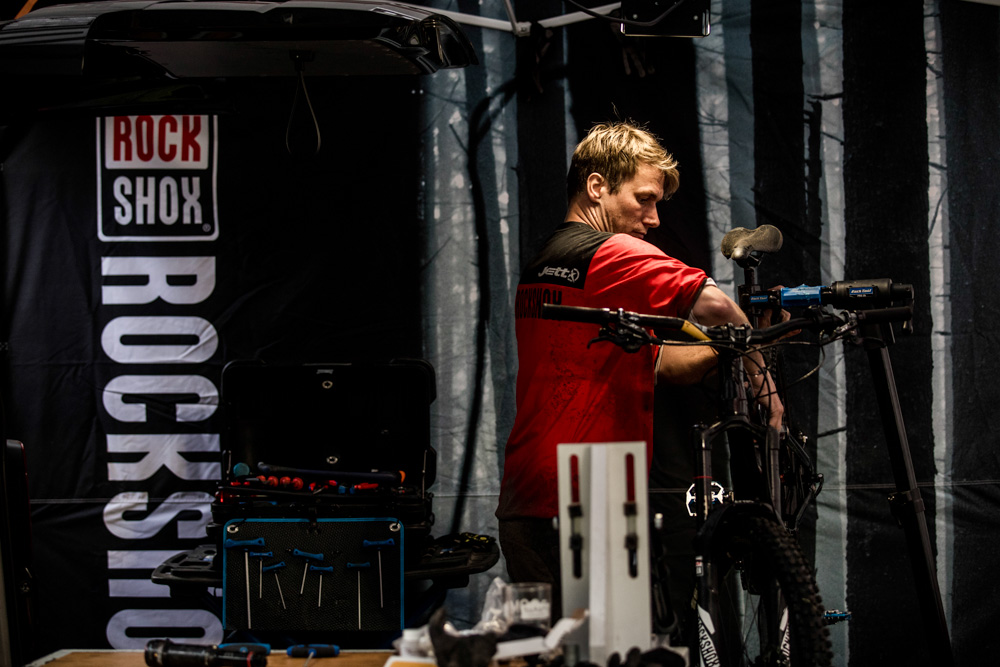
Numbers gleaned from the test trail are used to dial in the Mega
It’s in the trails
The most common location for SRAM’s UK tuning camp is at a trail centre open to the public in South Wales. It might not be the most glamorous location, but it ticks every box for this kind of work with a wide combination of terrain and trail conditions. Older, degraded tracks serve up relentlessly rough and rocky surfaces desperate to slow any bike’s progress, and lairy sections with deep compressions test bottom out resistance and support through the travel.
Dotted around the Welsh hillsides there are slower, steeper hand-cut tracks too – technical trails where fore and aft rider stability becomes more important and grip and braking traction is critical. Add in some classic faster, flowier trail centre descents and there’s the full gamut of terrain to mirror what potential customers will end up riding. To maximise test time, SRAM and the brands use a local uplift service to pump out the runs.
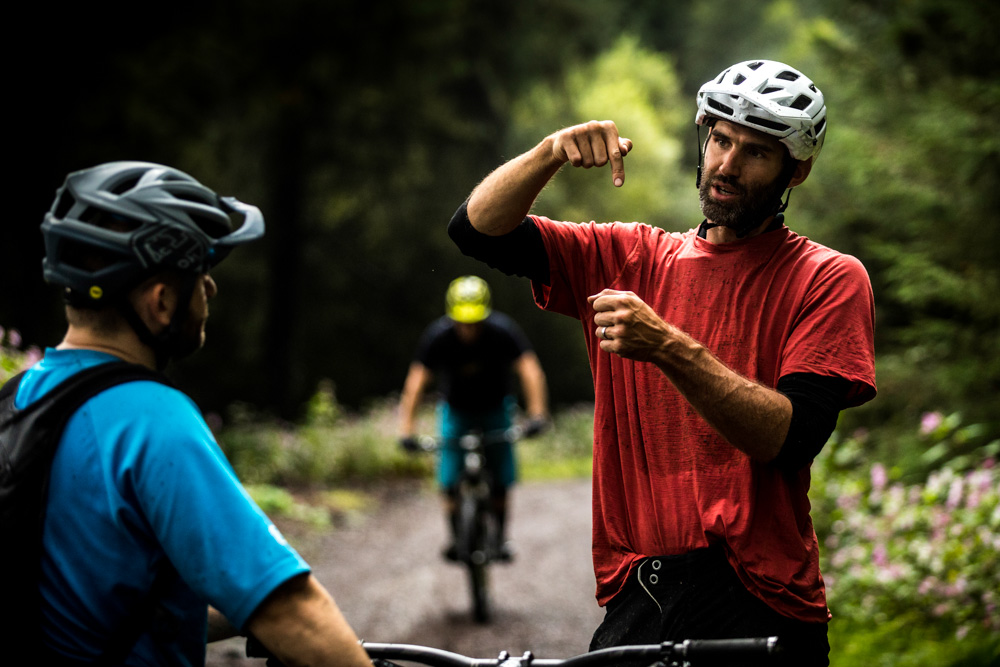
RockShox product manager Mandell is hand over fist the best man for the job
Team RockShox
Based on the valley floor with a compact, race-pits-style, EZ Up set up, RockShox rock up with latest generation suspension goodies and technical staff. For the Nukeproof session, two key personnel are Torben Borowy and Chris Mandell.
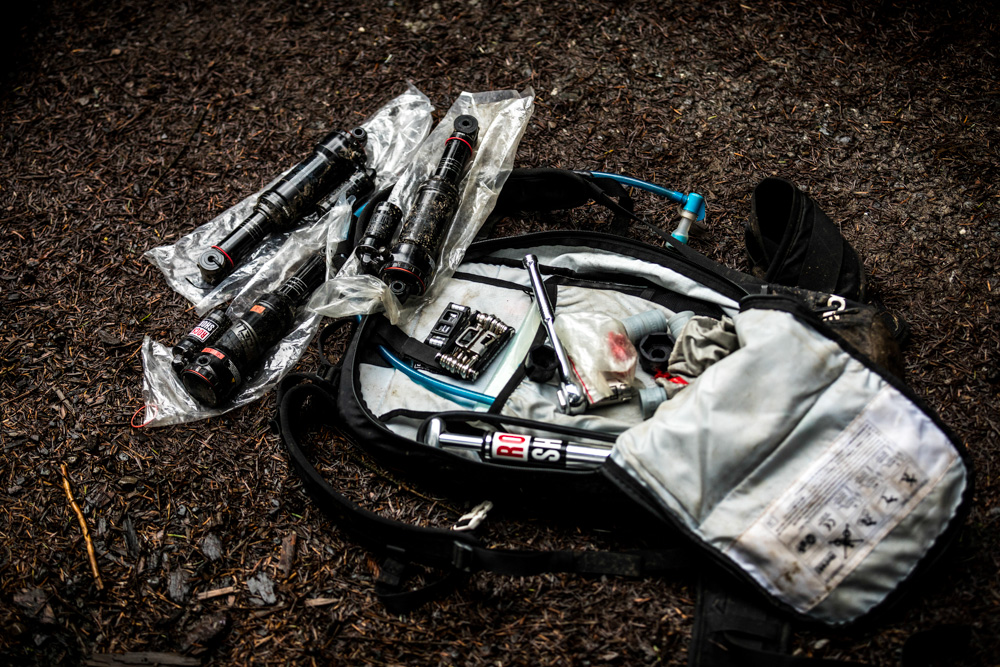
Factory fresh shock’s await calibration
German technician Torben is a super-experienced suspension boffin over from SRAM’s European HQ in Schweinfurt. He gets his hands very dirty riding hard and fast every day alongside the brands packing multiple suspension options in his fat backpack ready for immediate back-to-back trail comparisons. Torben is always hard at it, and, if the team aren’t out riding, he’s continuously building dampers or messing with shock tunes back at the pits.
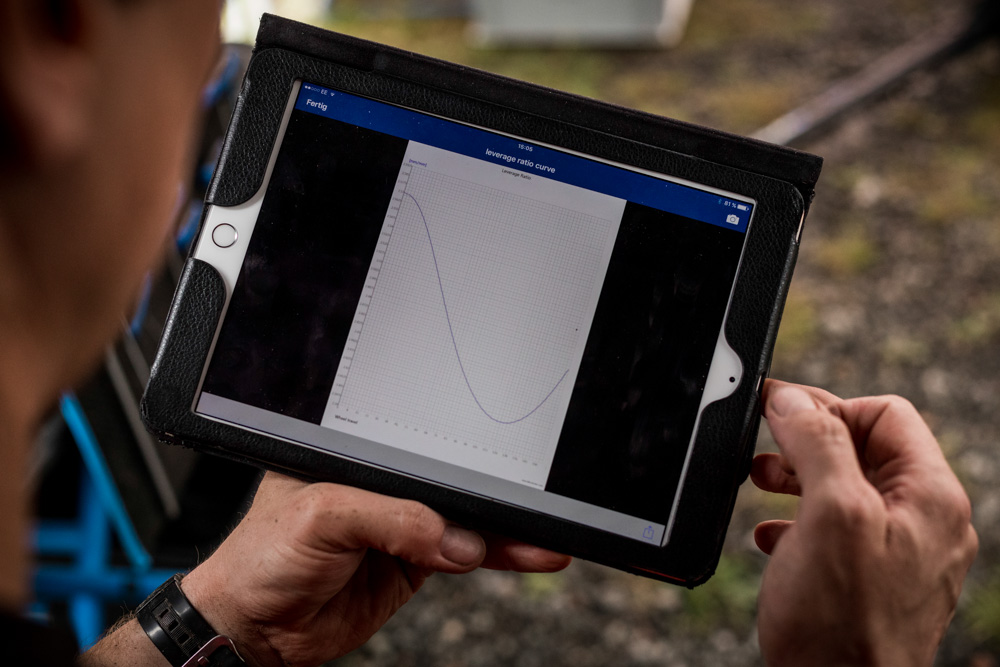
Playing spring curve Etch-A-Sketch
RockShox suspension product manager Chris Mandell (who also happens to be an absolute shredder) makes the long journey from SRAM’s suspension HQ in Colorado Springs, USA. Chris has worked developing the new dampers in the first place and perfectly placed to understand exactly how the products tick. The American happily drills into the inner workings of the shocks trailside and is presumably also keen to pick up on any feedback to keep improving the products SRAM develops.
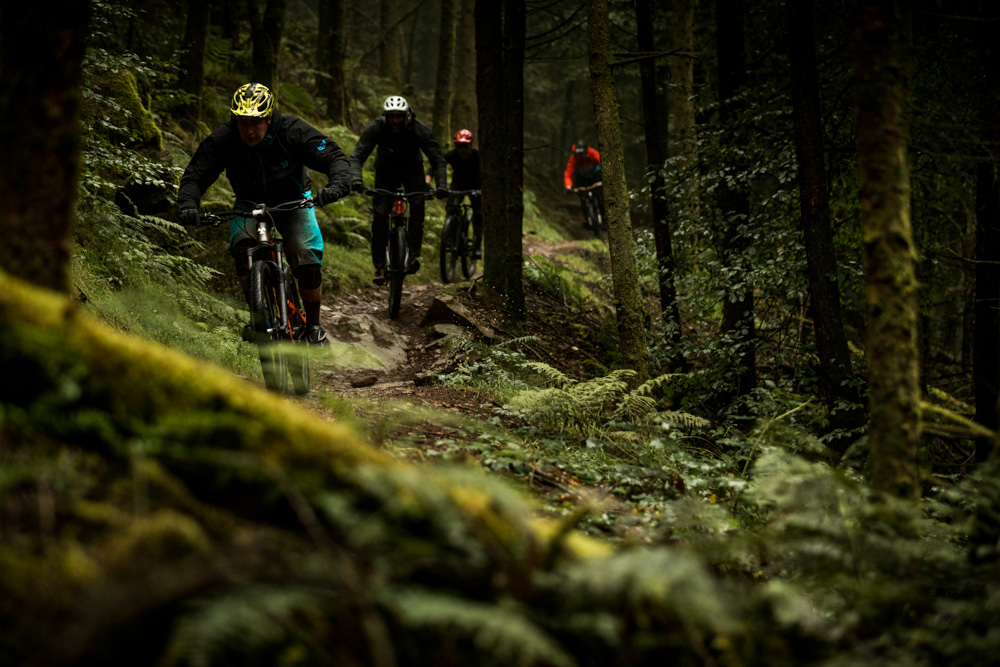
2D digital design + 3D reality check = cutting-edge suspension performance
On Nukeproof’s side, the test team here in riding kit might have seen any new products first hand in Taiwan (or digitally as images or drawings), but this UK camp is likely the first time they actually ride on the latest gear. Annual changes may be as subtle as a new manufacturing process, or as drastic as a brand new shock (and fork) with different chassis, damping architecture and springs. The bigger the changes, the more difficult it is to draw from previous knowledge, and the same’s true if a brand brings a completely new bike design to tune as well.
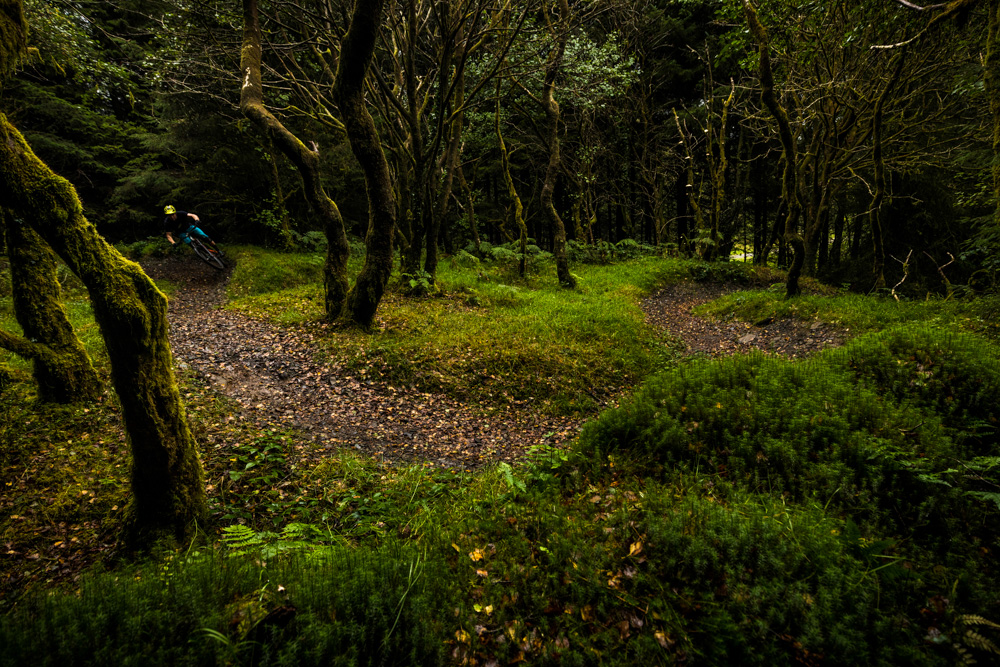
Tight, bermed turns are ideal for testing compression settings
Man versus machine
In theory, suspension products continually evolve and improve, but they still need to be perfectly tuned to bikes and riders, which isn’t always easy as multiple parameters shift. Geometry, wheel size, tyre width, suspension curves, chassis stiffness, fork offset and more all affect the system, and even the type of trails and tracks we ride continually changes too. Helped by the RockShox team, testers need to find the best balance of variables at any one point in time. The entire process can be seen as an amalgamation of a brand’s in-house understanding of its bikes and SRAM’s product knowledge and expertise.
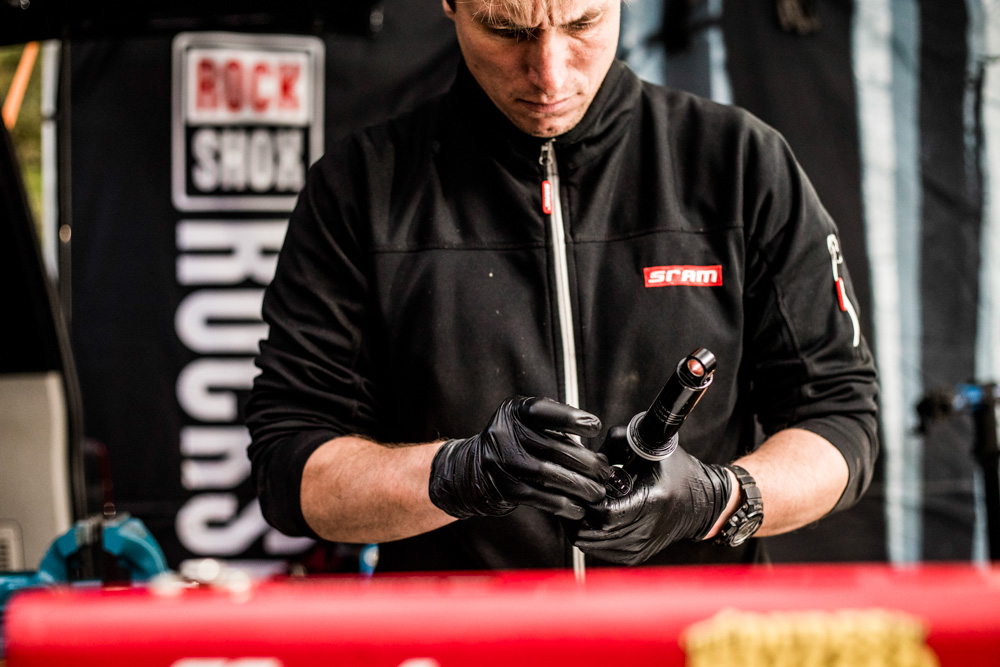
“Co-operate or the gloves come off” – Torben applies the shock treatment
Before any tyres hit the dirt, computer programmes model the exact leverage rate of each Nukeproof model and Torben prepares different shocks for each bike as a baseline. There are a confusing number of variables to juggle – compression and rebound tunes with names like L1, L3, L, M, H representing different damping forces (you might have noticed these on your own bike’s shock), and then different air can volumes, lockout force adjustments, and the ability increase or reduce progression in the spring on air shocks.
>>> How to set up mountain bike suspension
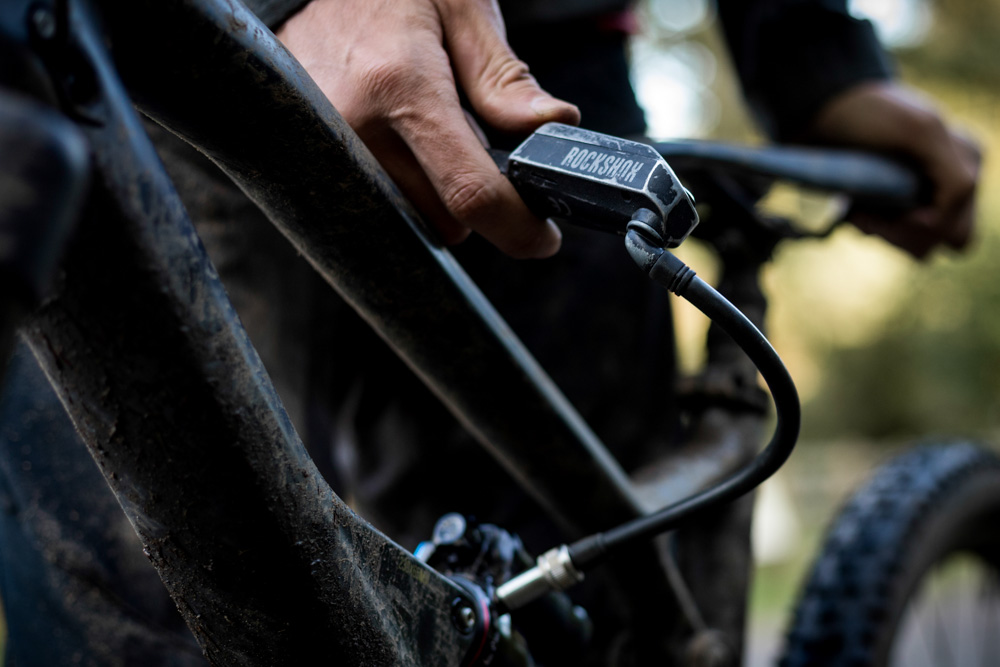
Using the same shock pump ensures consistency
Suck it and see
New products are developed on computers and sophisticated test rigs, but it’s only out on the trails suspension can be nailed as part of any new bike’s overall character. Back-to-back, repeated runs on the same track are the basis of any evaluation and ultimately it’s a process about personal preference. Testers rule out as many variables as possible by checking tyre pressures before every run, religiously setting sag on every different shock and also keeping well fuelled and fresh to try and discount tiredness or fatigue.
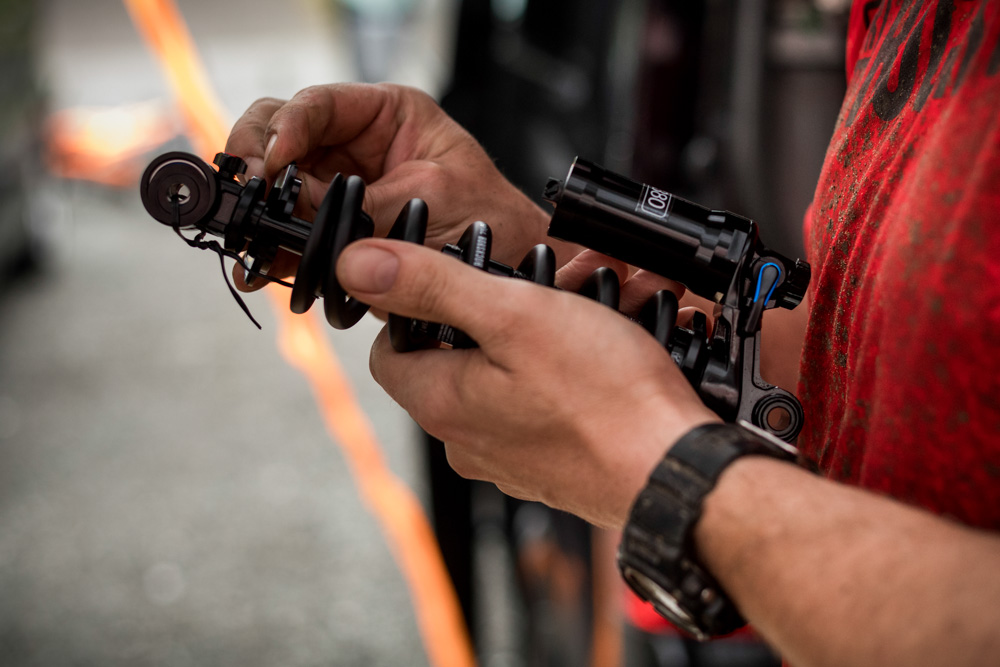
Does this mean a coil-sprung Mega is on the way?
Riders generally prefer to bike at around 80% on relatively short fixed test loops. This ensures repeatability and helps tune into the nuances of each bike on certain passages. The best test tracks mix a bit of everything from heavy compressions, grip-demanding wet roots and rocks, off cambers, big landings, pointy speed-sapping sections and even short sharp climbs. The tuning emphasis is most focussed on performance pointing down and along, but also takes in steep-in-places technical climbing to help assess chassis balance and stability.
Learning the flow of a test track helps the riding part becomes second nature and makes it easier to concentrate. Parameters like roll over, support, comfort, fun-factor, perceived speed, support when sat down climbing, smoothness under power and urgency when sprinting are all mentally balanced against personal experience and each individual bike’s aims and intentions.
A quick glance around at the bottom of a test run can reveal some intense technical babbling and jargon, often with Torben and Chris hunched over changing shocks for the next lap. Test riders frequently discussing infinitesimal details of a damper feel, try to predict improvements and swap damping tunes with colleagues so they can experience any sensations explained first hand. Some take notes or dictate into their phone. Looking in, it looks a lot like a few mates out for a ride, but in reality there’s a fairly intense search in action to pin down exactly what feels or works ‘the best’.
Shock tuning is a process of elimination as much as anything – does a change improve the bike or not? It’s detailed work that requires confidence, quick decisions and sensitivity to the exact ride feel. Once a test rider hones in on a specific tune, or prefers a previous one, the process moves a step forward. One tiny change can make or break a new model, so it’s vital to get it right. When a bike has been tuned to a certain track, the brands mix it up in the next session and try a completely different trail to ensure the suspension is versatile on different terrain too. Eventually, a consensus determines the best overall ride quality for the bike and potential customers.
The entire process normally takes a couple of days for a smaller brand like Nukeproof. Test riders might then have a chance to take a couple of shock options away (often hand built by Torben) to review at home before finalising any decision. Within a matter of weeks though, Nukeproof, like any other brand, has to press play, stick its neck on the line and commit to a shock tune. SRAM then inform its suspension facility in Taiwan, the order gets sent and, that’s it; the bike is signed off.
It can then be a long wait until the manufacturing and assembly process runs its course and product arrives back on these shores and faces judgement in the hands of bike testers and customers. Only at this point do the brands get to see if this fascinating, detailed R&D process has hit the nail cleanly on the head, or if they’re left with bloodied thumbs and empty order books.
Q&A with Nukeproof’s Dale McMullan and Rob Sherratt
Each brand typically brings a small number of test riders to do the shock tuning – for Nukeproof, two key testers are R&D boss Dale McMullan and marketing manager Rob Sherratt. Dale and Rob talked us through the annual SRAM tuning process from Nukeproof’s perspective.
MBR: How important are the SRAM suspension tuning sessions to the final ride quality of Nukeproof bikes?
Tuning camps with SRAM are crucial. We get a good starting point working closely with SRAM/ Rockshox in development and a base setting from Leverage rates and curves. But, these bikes don’t live on paper and actual testing in real world environment is crucial to creating the feel we want on our bikes and perfecting the correct tunes. The test is also an awesome opportunity to have the knowledge and experience of SRAM’s test team to help fine tune the ride of our Rockshox bikes
MBR: What kind of things are you looking out for/to achieve during the tuning camp?
Being able to provide our (customers) riders with the best performing Mega possible for the following season. Out of the test we plan to finalise the correct shock tune and air can volume options for the all the new shocks for each new Nukeproof Mega models.
MBR: What are some of the hardest things (if any) to nail down in terms of suspension feel/balance?
With modern shocks one size doesn’t fit all and the hardest thing is striking the correct balance. With shocks improving so much and becoming much more tuneable, we aim to offer a really good base setting that rides well out the box. Each rider/ customer has the potential to optimise the settings due to the number of variables effecting shock performance such as riders weight/ riding style/ pedal preference/ terrain etc.
MBR: How far in advance do you find out about new products/developments, and how long to you have to adapt something like a Metric shock into the Nukeproof product range?
On average we get a 12-18 month window to know what’s coming. On rare occasions; such as with the new Metric sizes, we had slightly longer and were provided with the new shock dimensions to ensure we had enough time to meet release dates. However it is crucial that we have the opportunity to test any new standard/ sizes to see what the performance advantages are, before specing on any Nukeproof.
MBR: Do SRAM help you choose starting points on suspension tunes? How close is the relationship in terms of sharing suspension leverage data, etc.?
We have a good idea from the outset on what damping ranges will work and the ride characteristics we want to achieve, but SRAM/ Rockshox help a lot also. We supply our kinematics in advance and in this case sent Sram/ Rockshox a sample bike, to get another opinion. From here we work together to perfect the ride character we want. We will then test some sample tunes a number of months ahead of meeting up at the camp where we perfect the tune together.
MBR: Is there only so far you can go with modelling and analysis and that it’s crucial to tune suspension in the real world with real riders?
It’s a good starting point, but nothing can replicate real life testing, a leverage curve won’t show all variables- suspension balance and different load inputs eg standing, seated saddle down, seated saddle up.
MBR: What makes for a good test rider?
Being able to notice and feed back the feelings that they are noticing- no matter how small/ subtle the changes are. This may come from experience on the bike or a knowledge of the characteristics of design.
MBR: How does the EWS team and riders like Sam Hill feed into the equation for the public?
Having an experienced team and a legend like Sam Hill test our bikes is crucial to the overall package. Its awesome that SRAM support the team so this can help massively providing the best products for our riders/ customers. They do have slightly different needs of the bike, but their experience is crucial in the development of the bikes. We tested with them just after this camp in a separate Rockshox/ Sram test from a blank sheet of paper. With no previous knowledge in a blind test it was a nice surprise Sam came up with the exact tune for his Mega 275c that we had chosen at the production test- the only difference in Sam’s shock from the production bikes is that he chose to run 2 volume bands to keep up the progression.
\
We’ve been coming here for years, its great to be able to feel the progression year on year of the bikes on similar terrain. Afan has an awesome variety of trails too, steep climbs, flat single track, fast rough sections with high speed hits and G out compressions, If you have any over damping or shock stiction problems this track will tell you! Added bonus of the lodge being a good place to enjoy a post ride ale too.
MBR: Does a UK manufacturer have specific requirements to match our UK trails/climate/terrain?
It’s a tough one to be honest- we try and test in all terrain, so try and mix testing with our riders around the globe. We want our bikes to work well at super fast open alpine descents as much as they do on wet rooty technical trails- this is where the race team really comes into its own (as the variety of trails that the EWS is on really helps test). But not much beats wet slippery, rooty conditions in the UK where the bike has to find grip! A badly tuned shock or fork here will have you on your ass!