How does 4.5kg for a complete bike sound?
It looks like the honours for lightest mountain bike in the world might actually lie at the door of one Seb K. How does 4.5kg for a complete bike sound?
>>> 10 of the most outrageously expensive upgrades for bikes
It seems we opened up a can of worms by featuring Gustav’s über light Scott builds recently. It seems that these are not the lightest mountain bikes in the world, just probably the lightest 29ers in the world. Seb K, just like Gustav, is pretty well known in the world of the weight weenie and over the past few years has been churning out some crazily light builds.
Seb’s lightest mountain bike
Seb’s approach is a little more hands-on than many other light bike builders. Preferring to get down and dirty modifying and manufacturing his parts, Seb hasn’t just cherry picked the lightest exotic upgrades.
Now some might say this puts him at a distinct disadvantage but it looks like the London based bike fettler relishes the challenge of transforming some quite ordinary parts into objects of modified beauty. His current, rather bonkers build is a four and a half kilo rigid 26in wheel mountain bike based around a Planet-X carbon frame. Hardly a mega bucks featherweight.
You can follow and keep up with Seb’s work through his Blog, Facebook page and Instagram.
mbr caught up with Seb to find out just what motivates him to create these machines.
What motivates you to create these light bikes?
Seb: The challenge. The building process of making a light part or modifying a component and working with light materials – I just love carbon.
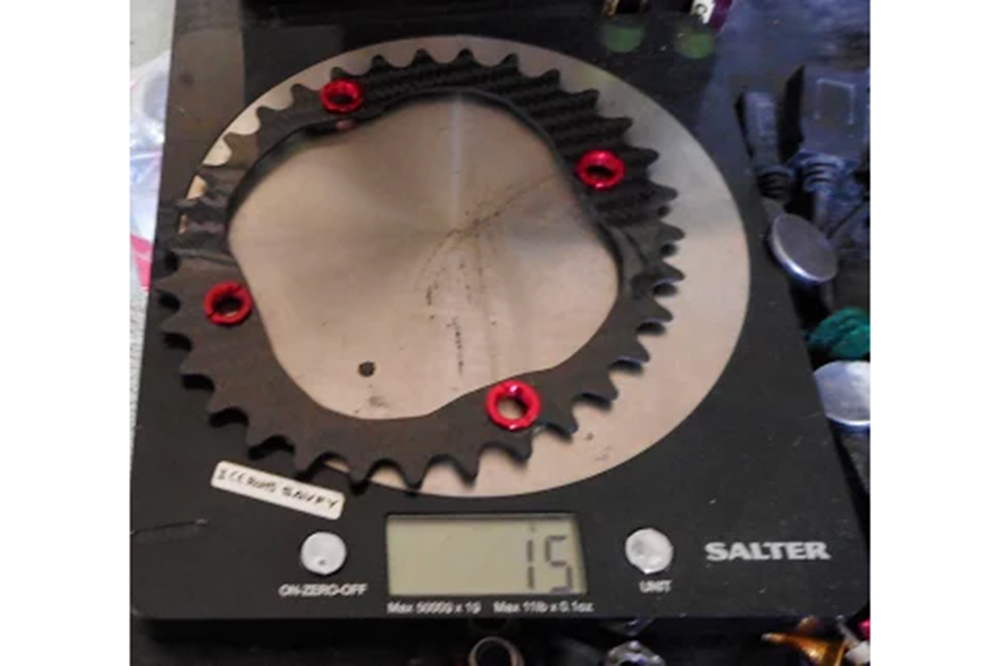
Seb hand makes his own carbon components including this 15 gram chainring (including bolts!).
When did you first feel the urge to modify your bikes and why?
Seb: I first started modifying components to get them as light as possible because it involved a lot of machine work and also to see what weight I could reduce them to. I then discovered the Weight Weenie websites and was amazed by the bikes I saw and took it on as a challenge. I get a buzz from making something myself and I love a machine that I can ride and pick up with one finger. I also love having a custom bike no one else has.
Can you remember what the first component you modified was?
Seb: This is hard because I make so much stuff but if my memory serves me correctly then it would be a set of old pedals. I machined them down, first the pedal body and then hollowed out the axle.
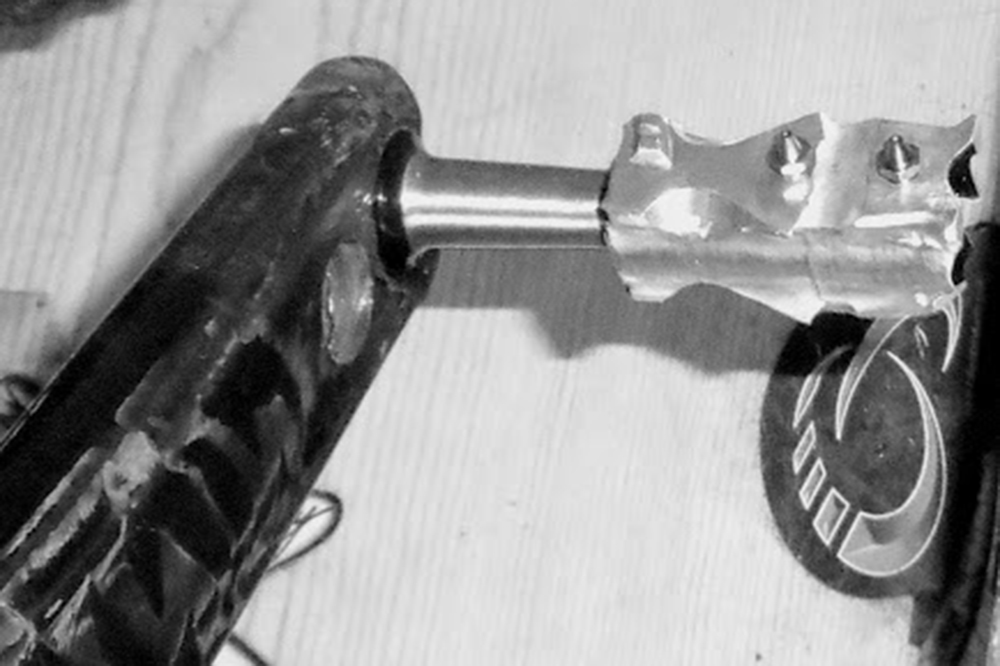
Pedals are a particular forte of Seb’s modification prowess.
Talk us through your thought process when it comes to creating a build. Do you have a clear idea as to component spec or is it more of a fluid approach with choosing parts?
Seb: I have a rough idea what to go for. But it really starts with a light frame that I can do some work on, then I take it from there. I can never picture a full build in my head from the start.
What about the frame? It looks like you haven’t just gone ‘What’s the lightest frame on the market?’ Are there other constraints you consider?
Seb: It was a fairly light frame to begin with but I found ways to get it lighter. First small things like removing the cable guides and sanding down the clearcoat. Then more complicated things like BB machining (as I have a shorter, carbon crank axle which I also made), reinforcing the down tube and removing all bosses (there are no bottlecage bosses or anything else on the frame). Also I had to cut away a small section from the chainstay to allow clearance for the chainring and then reinforcing that with Kevlar and carbon filler. The weight limit has been slightly reduced for the frame and absolutely no jumping of the bike is allowed.
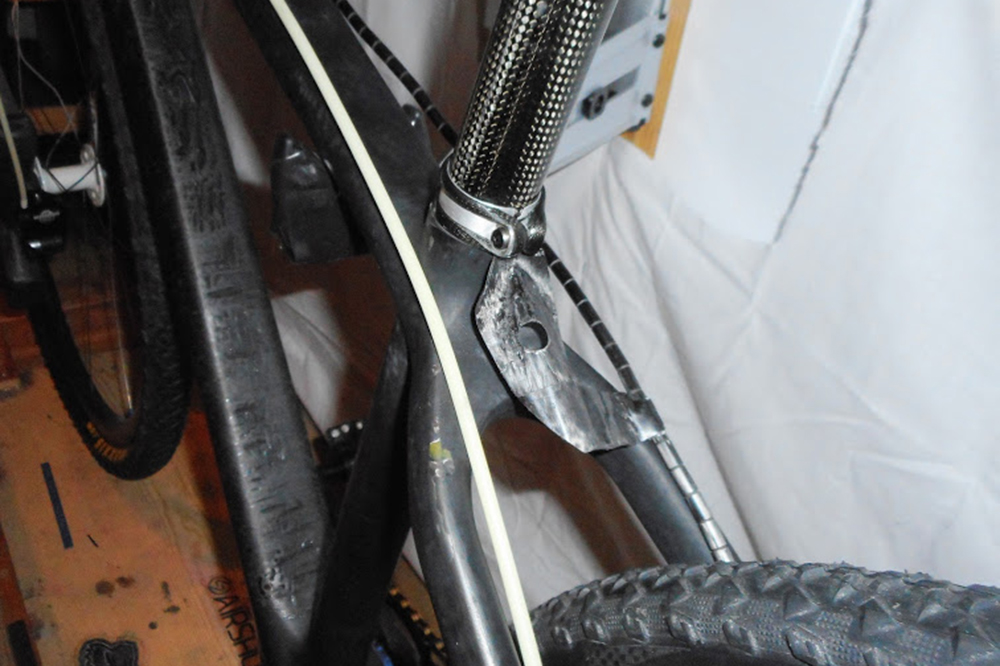
The Planet X carbon frames been cut, trimmed and modified to make it completely unrecognisable.
It looks like you tend to focus on modifying parts also, rather than just spending out on the lightest kit available. What made you adopt this approach?
Seb: I love building things and so if I can modify a component and get it the same if not lighter than a manufactured part then I will do it. For me the custom way is the only way.
One look at your builds and there is barely a recognisable part. What makes you look at a component and think, ‘I can make that better/lighter’?
Seb: I guess it’s the dedication of being a full on weight weenie. I just get that itch when I see a component and want to get at it.
Do you do a lot of prototyping?
Seb: Oh absolutely. I have spent a lot of money on materials to make prototypes. I have been lucky to get a component spot on first time but not very often.
Have you had any catastrophic failures in the prototyping phase?
Seb: I wouldn’t say catastrophic but the odd crack now and then. If it’s metal I have to start again but with carbon I simply repair it.
At what point do you look at a part and think that you are happy with it?
Seb: When I have gone over every section and cannot see any other way to get it lighter.
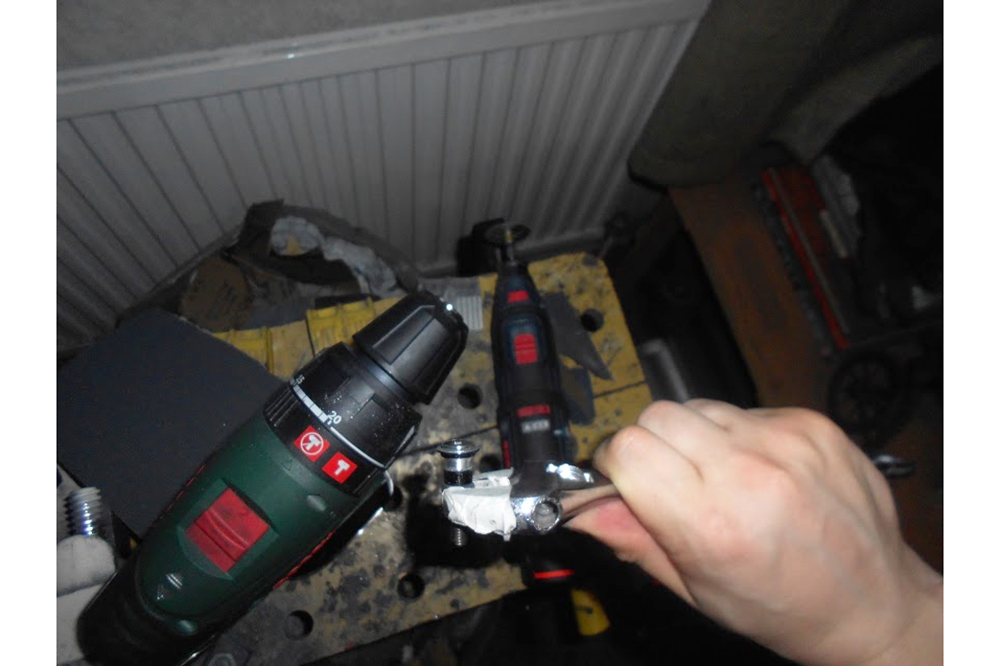
Seb spends many an hour with the drill to get parts exactly as he wants them.
There looks to be a lot of precision machining and manufacturing of components that looks way beyond the skills of most average riders. Do you have an engineering or materials background?
Seb: I don’t, just years of reading books and teaching myself new skills. Trial, errors and practice.
Talk us through your lightest current build. What frame is it based around?
Seb: Frame – Planet X carbon frame | front section downtube cut out and bosses removed then further hollowed and wrapped with 12 layer UD (carbon) and Kevlar Twaron mix fabric | rear dropouts cut away and new ones machined further along and gear hanger removed and excess reinforced with layers of UD and Kevlar Twaron fabric | all cable guides removed | spacing issue with chainstay and chainring so section cut away and reinforced with Kevlar and carbon filler | seat stay carbon top layers machined away and replaced with lightweight matt black vinyl | rear brake boss barrel nuts replaced with aluminium barrel nuts taken from a set of Tune skewers and new threads tapped | bb cups machined around 1.8mm to allow shorter crank axle to fit
BB – Token blue cups with ceramic bearings and Ti Nitride cups and races | spacers removed and replaced with custom made driveside carbon spacer | seals removed
Headset – Nukeproof ceramic | seals removed
Fork – DT Swiss carbon fork | legs shortened and reinforced with epoxy resin | dropouts heavily machined and hollowed out further | brake mounts removed and aluminium threaded rods (made from two aluminium bolts) inserted and epoxied into place | legs hollowed out further and caps removed and machined off | clear coat and paintwork sanded off halfway down | steerer shortened
Fork race – custom made Extralite red race for 1 1/8 to taper | custom blue race for headset top bearing
Seatpost/saddle – Schmolke TLO post and Extralite Hypersaddle | seatpost shortened and head removed | carbon fibre plug with flange made and inserted and epoxied into seatpost | saddle shell machined into new shape and cutout made with cream overcoat sprayed on nose | cutout reinforced with UD fabric | saddle rails removed and undershell sanded down | post and saddle epoxied together
Seatclamp – Tune Wurger Skyline 2 | grub screw replaced with titanium gold grub screw
Stem/handlebar – Schmolke TLO bar and MCFK carbon stem | bar shortened and clearcoat sanded off and carbon polished | stem faceplate and fixings removed | stem front cut away and lightly sanded | bar and stem bonded with Kevlar Twaron fabric | stem fixings replaced with custom blue fixings
Grips – custom Extralite grips in white | shortened and highly tapered in the lathe
Top cap – Carbonice carbon cap | cap machined down to be flatter and internal sections sanded down
Crankset – Race face carbon cranks | clear coat and paint sanded off (except inside driveside arm) and carbon polished | axle machined off and custom made carbon axle fitted | granny bosses machined away | crank bolt threads machined off and widened insert | hole bored near pedal eyelet | holes perfectly drilled on crank arms | custom made bearing shims wrapped over axle bearing contact points | arm ends shortened and reinforced with UD and Kevlar Twaron fabric
Crank bolt – custom titanium Ti Nitride coated bolt specifically made for Raceface cranks
Pedals – KCNC Knife pedals | heavily machined down pedal platforms and all anodising removed | sections machined away from platforms | polished surfaces | two holes drilled on each pedal platform and 4mm threads tapped | custom titanium pedal pins shortened in the lathe and fitted to pedal platforms | axles removed and DLC coating partly removed in the lathe | titanium end bolts machined down in the lathe | axle threads shortened and rounded in the lathe
Chainring – handmade carbon chainring 32t oval | custom red chainring bolts pressed into holes
Chainring bolts – custom green chainring bolts
Sprocket – handmade carbon 14t sprocket | drilled holes between each tooth | titanium ring machined with splines and epoxied onto sprocket
Chain – YBN titanium chain Ti Nitride coated | shortened
Wheelset – custom carbon rims made in Portugal with white hubs | three rear hub disc tabs machined away | spokes replaced with titanium | nipples replaced with blue Sapim aluminium nipples | less spoke count but fully tested and successful | valve holes slightly widened and surrounding reinforced with carbon kevlar fabric | spoke holes slightly widened with Velo Plugs inserted
Discs – custom carbon discs ceramic coated
Disc bolts – Rear Extralite hollowed tapered bolts | front Schmolke bolts shortened in the lathe and heads machined down and tapered
Front skewer – skewer removed | 6 mm threads tapped into wheel axle end caps | two Extralite caliper bolts machined down in the lathe and fitted
Rear skewer – Tune U20/Carbon Ti mix | Tune U20 rod removed from assembly and shortened in the lathe | CarbonTi lever removed from assembly and shortened with a new shape machined and laser etching removed | CarbonTi end nut heavily machined down in the lathe and highly polished | CarbonTi lever and end nut fixed with TuneU20 rod and washer for complete rear skewer
Brakes – Brakeforce One | hoses replaced with glow in dark hoses and shortened | valves replaced with custom blue valves and fixings | bore caps replaced with black/blue aluminium caps | lever mounts replaced with Magura MT8 carbon mounts machined down and eyelets countersunk | bolts replaced with Schmolke carbon bolts shortened in the lathe and heads machined down, tapered and countersunk | rear caliper bolts replaced with Schmolke carbon bolts shortened in the lathe | front caliper bolts replaced with KCNC scandium gold nuts shortened in the lathe (nuts fixed to custom threaded rods made in the fork – look at ‘fork’ description) | lever replaced with handmade carbon levers finished with blue threaded reach adjusting rods (made from two aluminium bolts) rounded ends in the lathe | lever bolts replaced with Schmolke carbon bolts shortened in the lathe | lever gold bolt nuts made from two chainring bolts machined down in the lathe and 6mm thread tapped | handmade carbon prepreg pad plates made with neodymium magnets epoxied into place and cork fitted for pads (still testing) | custom titanium pad pins made specifically for the BFO brakes with anodising removed in the lathe and highly polished
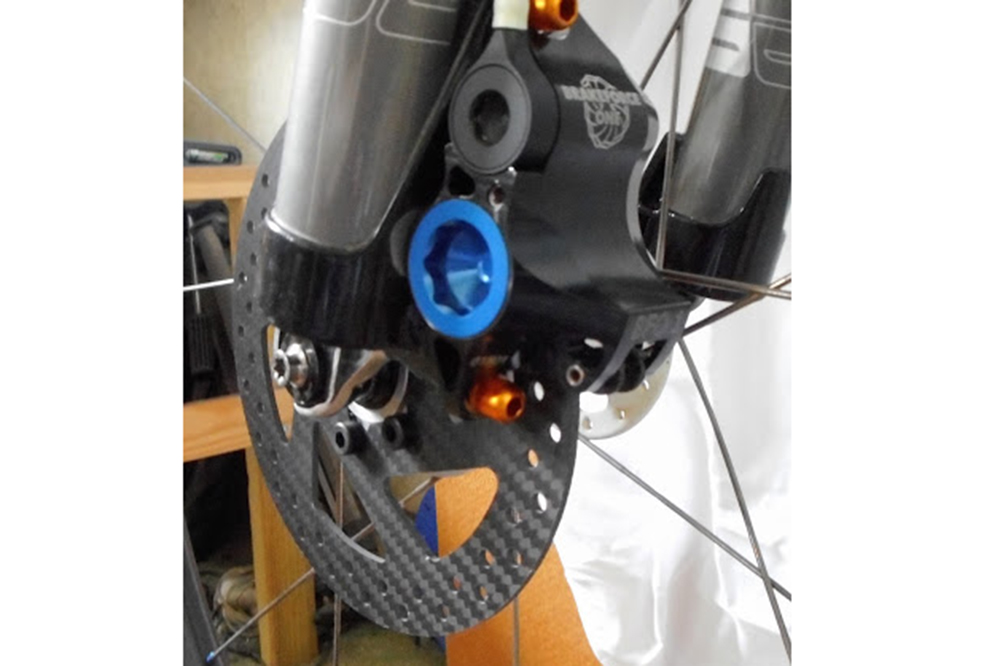
Brakeforce One provide the brakes. Yep, that’s a custom built carbon/ceramic disc.
Tubes – Tubolito S-Tubo | valves removed and replaced with custom carbon valves | carbon valve ends cut off and smoothed in the lathe | main tube valve inserts roughened up and slightly shortened | carbon valves attached to tube valve ends with 6 layers of UD fabric (still testing)
Tyres – Maxxis 285 tyres
How light have you got it?
Seb: The lightest is at its present state of 4.540kg
You go to the tiniest lengths to shed grams, take your inner tubes for example, you modified them didn’t you?
Seb: Yup! They are Tubolito S-Tubo tubes. I could easily see the valves being the part to modify as it’s the only part that won’t damage the tube and for its size is the heaviest part. I had some carbon valves from another build and I machined the ends and machined down the excess valves on the tubes. I used UD and Kevlar Twaron fabric to bond the two parts together. I removed the presta valves and drilled into the carbon valves to remove any excess material and then sucked up the debris . They are the lightest MTB tubes in the world at 43grams each. Nearly a month since inflation (36psi) and they have lost around 30% air which is incredible. Tubolito and I were communicating and they said they would be looking at the valves for the future.
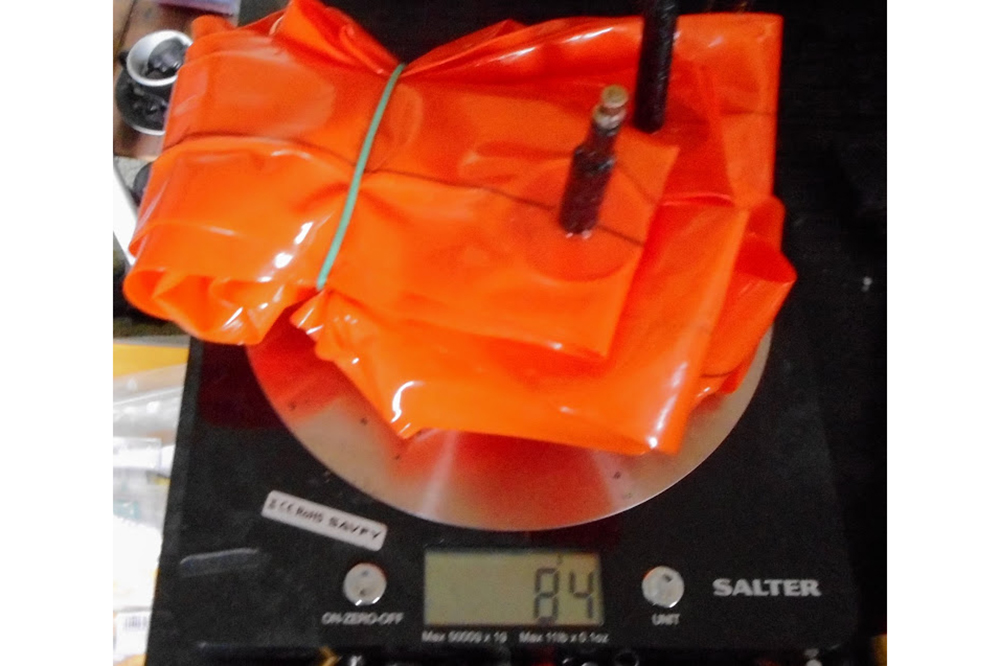
Tubolite inner tubes have been further modified with carbon valves.
Even more amazingly you made your own carbon bolts, how do you go about that process?
Seb: I have a tap and dye kit. I use the lathe to make the stems and then machine the heads to shape and use the dye to cut the threads. Unfortunately I don’t have a machine to make them rolled so they are cut but still strong. You need 0.5mm difference of the size you are making to get a nice deep thread. Make sure you don’t machine too close to the head and leave a nice wide shoulder so the head contact is strong.
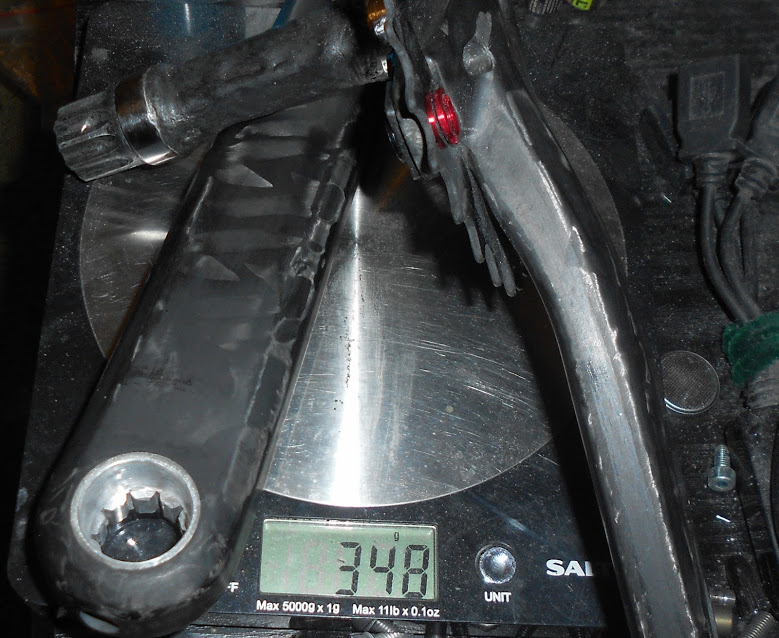
The Race Face cranks with their custom carbon axle are a particular favourite of Seb’s.
Which area of the build are you most proud of?
Seb: I’ve been asked this before. Definitely the cranks. The carbon axle took ages to get right and was a few days work just to get one side done.
Where did you find you shed the most weight?
Seb: The saddle and post combo. It’s around 74grams all in.
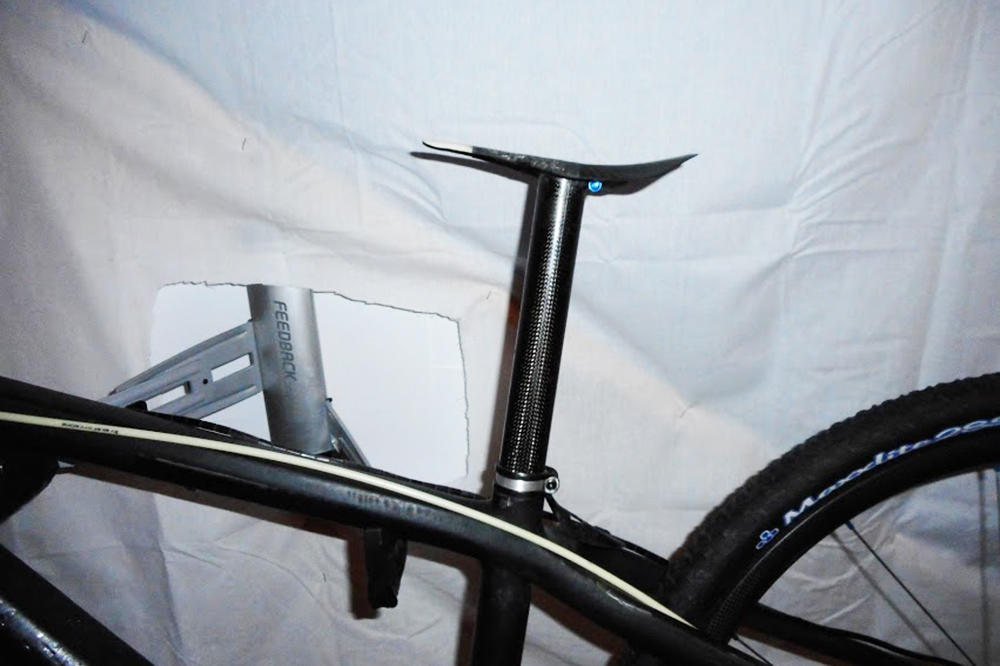
Seb managed to reduce the saddle and seatpost combo to just 74 grams by removing the rails, changing the shape of the saddle and bonding the post to the saddle.
How much time do you think you have spent on this current project?
Seb: It’s been over a year for sure.
Many readers will take one look at the bike and think it will just collapse if taken off road. Have you ridden it and where?
Seb: A few have said it would break. I have had a few nasty comments and have had a few arguments in the past and in the end I just stopped responding. It seems people see these bikes and think because it is light it will break, rather than thinking it is light and with advancements in materials and techniques it will survive. I have taken it to my local park and ridden on the trails there. Not too rocky but a few high stumps that I have slammed the bike into (on purpose!)
Talk us through some of your other bikes, as this isn’t your only build. Do you have anything more appropriate for offroad use?
Seb: I have a full suspension carbon bike that weighs 6.5kg. That in itself has had a lot of work put into it including a shortened Lauf fork (lots of carbon fabric used for that), sanded down Scott Spark Limited frame, alcantara Tune Speedneedle (new edition), handmade alcantara grips from Germany, Reset Racing pedals that I have modified so much you will need to look at my G+ page to see what I have done, carbon 15mm axle modified in the lathe, Scrub rotors, modified Darimo seatpost fixings, custom Extralite chainring with a rare coating, one off titanium sprocket from the States, modified Easton rear hub, carbon DT Swiss carbon shock with lever removed and hex shape stamped into place (hex key used to save weight), Magura MT8 brakes with custom gold aluminium connector fixings and blue aluminium screw thread lever bolts (made in Germany), sanded down FSA carbon cranks with granny ring mounts removed, blue Chris King headset, Tubolito inner tubes, YBN titanium chain ti nitride coated, Extralite stem with all anodising removed, a carbon steerer extension that I made to increase the length of the steer as it was a little short and re-laced carbon wheelset . I also have an electric fat bike that has had a ton of work including a carbon fork, carbon railed saddle with built in elastomers and shortened BB shell to allow the use of a Shimano Saint crankset.
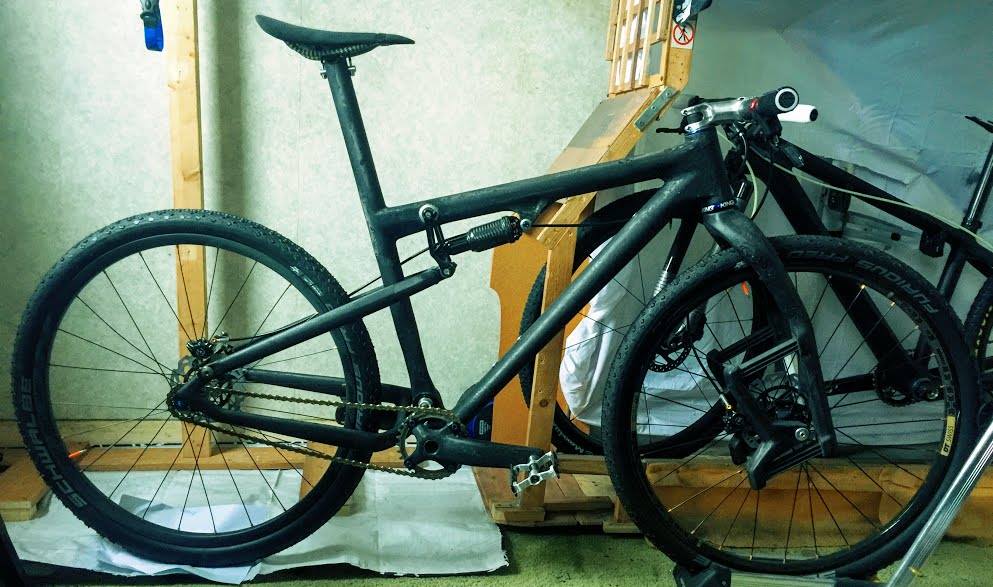
Deb’s other build is a super light Scott Spark.
Then there’s my fully rigid SingleSpeed electric bike with a very custom full titanium freewheel (screw thread) and all Ti nitride coated, shortened wiring, titanium blue axle nuts, aluminium axle spacers, MCFK seatpost, Tune Alcantara Komm Vor + saddle, magnesium pedals machined down with full Ti Nitride titanium axle further hollowed, Middleburn cranks, custom blue chain tensioner with blue ceramic tension jockey wheel, Magura MT8 brake with custom gold connector fixings, custom white Extralite grips machined down in the lathe (right side shorter to accommodate the throttle), Easton carbon handlebar, Tubolito tubes, re-laced rear wheel, front Easton Haven wheel and all cable guides machined off the frame then primed and painted .
All of your builds look to be based around a singlespeed drivetrain. Have you thought about any geared options?
Seb: The bikes used to be geared and I still have two sets for a future project. They have also been modified to death and include a modified Campagnolo full carbon derailleur with Schmolke carbon bolts, handmade Kevlar jockey arm plate, aerospace delrin jockey wheels with full ceramic bearings and sanded down cage, blue Powercordz cables, machined down XT derailleur with a carbon jockey arm, aluminium fixings and carbon clutch cover bolts, Nokon full carbon housing, modified XT shifter with clamp machined off and Brake Force One twin mount used with Extralite titanium bolt, different modified XT shifter with custom, handmade carbon cover plate and modified clamp mount.
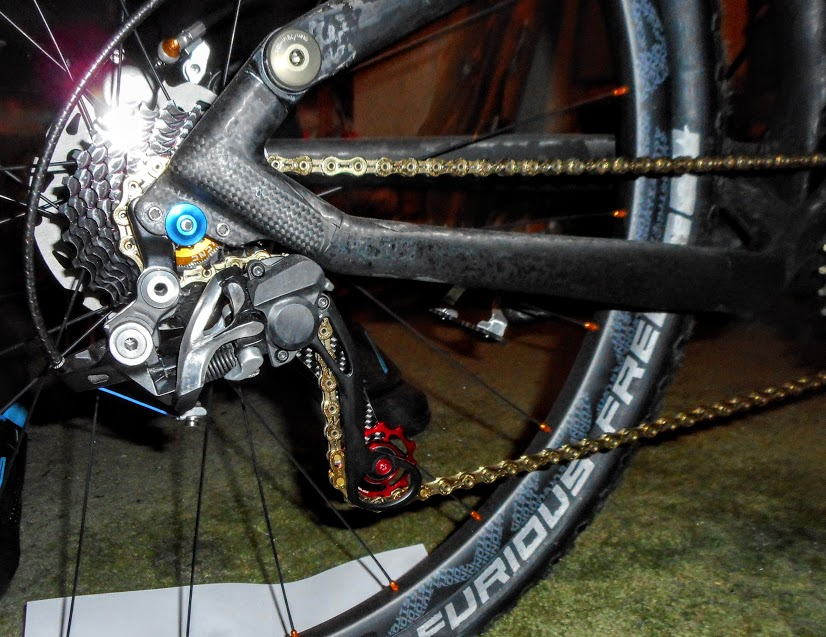
Seb has geared options for his builds if he so fancies. Obviously the weights go up though.
Are there any production components that you think are perfect as they are, or could everything be improved?
Everything can be improved. Manufacturers always make parts to exceed limits to cover themselves and don’t necessarily need to be as overly built as they are.
Do you have any advice for someone that might be inspired by your handy work?
You need lots of patience for this kind of work. Get some books and read up on machine work, metal work, carbon building and be prepared to invest a lot of time and (of course) money.