The Athertons are mountain biking royalty, so their eponymous bike brand comes with the ultimate seal of approval; we head to their Dyfi Bike Park testing ground
The Athertons are mountain biking royalty so their eponymous bike brand comes with the ultimate seal of approval; we head to their Dyfi Bike Park testing ground.
The Athertons need little introduction, but they certainly deserve one. Dan, Gee and Rachel Atherton have been a dominant force in UK gravity racing for over 16 years, and are as close to a household name as it gets in mountain biking. Individually they’ve had more podiums than many race teams, and in creating events like Red Bull Hardline they have helped to push mountain biking’s boundaries, while at the same time making it less of a fringe sport.
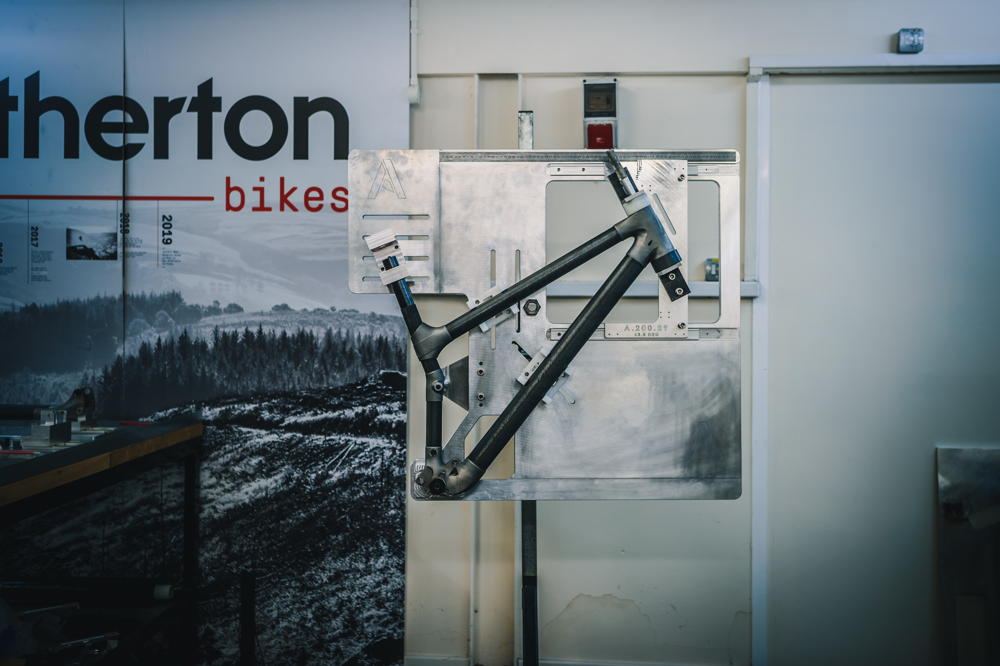
Atherton Bikes: old school aesthetics meets cutting-edge technology
Over their careers the Athertons have raced for the likes of Muddy Fox, Giant, Commençal, GT and Trek. Last year, however, they decided to do something different. Rather than sign up to another frame deal with a big-name brand, they created their own bike brand and put their hard-won race experience to work, producing a range of bikes worthy of their name.
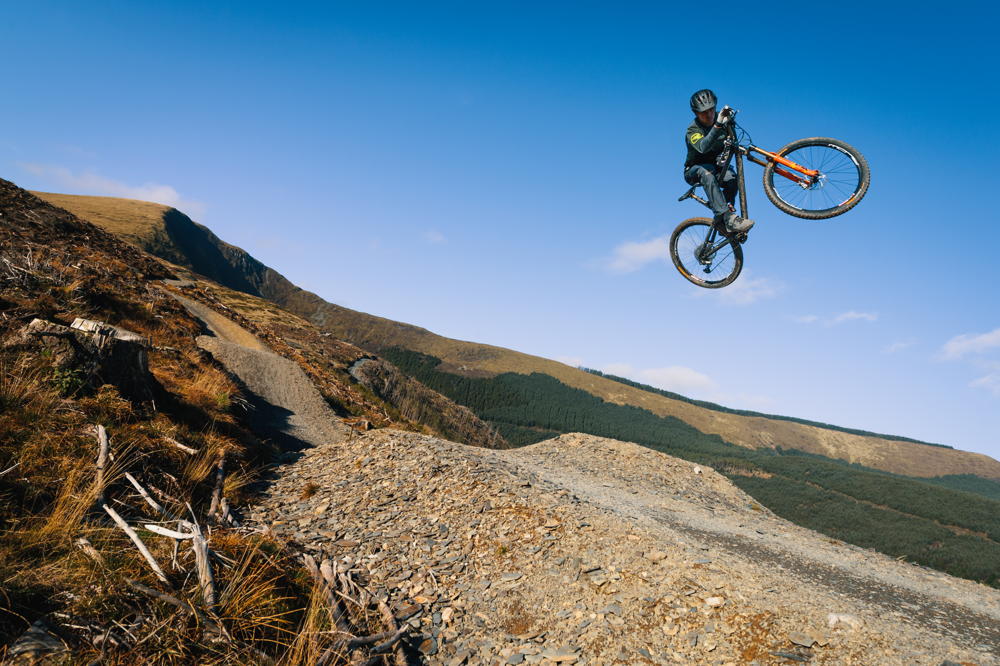
Dan’s the man for getting new designs off the ground
It would have been easy for them to have just called up a factory in Taiwan and ordered a bunch of frames with Atherton graphics emblazoned on the down tube. But this project was about more than that. It was about doing things their way — pushing limits, trying new ideas and using technology to their advantage. Working with a sponsor always involves a bit of give and take when it comes to product development, but by being in control of every aspect of the frame’s design and manufacture, the team could ensure they were working without compromise to make the best bike they could.
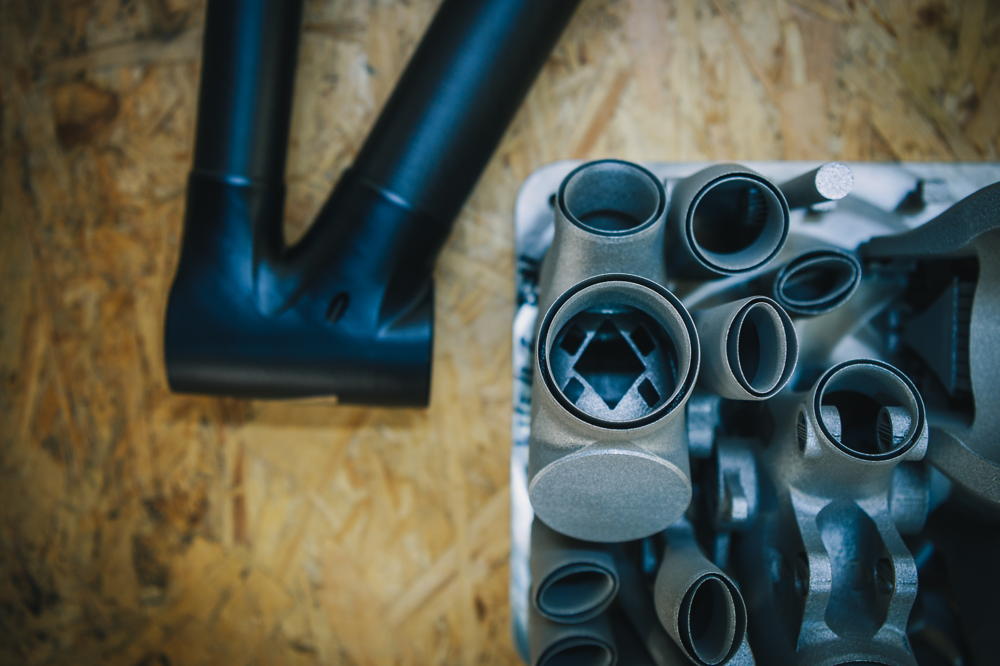
3D-printed titanium lugs are bonded to carbon tubes
There are no signs on the side door of the unassuming business unit on the outskirts of Monmouth. From the outside, Atherton Bikes HQ is a low-key affair — it’s what’s inside that counts. A downhill bike is held in the upright frame jig and the first batch of 150mm-travel, 29in enduro frames are being meticulously pieced together in the assembly area. Running the length of one wall is a poster charting the Athertons’ careers to date. The feel in here is definitely less bike workshop and more race garage — unsurprising really. Shelves are full of all the parts needed to make any bike company work, as well as mud-covered wheels and used bike components. Of more interest are the lengths of carbon tubing and what look like intricate sculptures neatly lined up next to taped-off workstations.
F1 influence
Visually, the Atherton Bikes frames are unlike anything else. The combination of composite tubes joined by 3D-printed titanium lugs makes for a unique look, but the reasons behind this assembly method are rooted in engineering know-how rather than aesthetic whim. The design team behind the frames have backgrounds in Formula 1 and the aerospace industry and when working out the best way to manufacture a mountain bike frame they looked at previous projects outside of cycling.
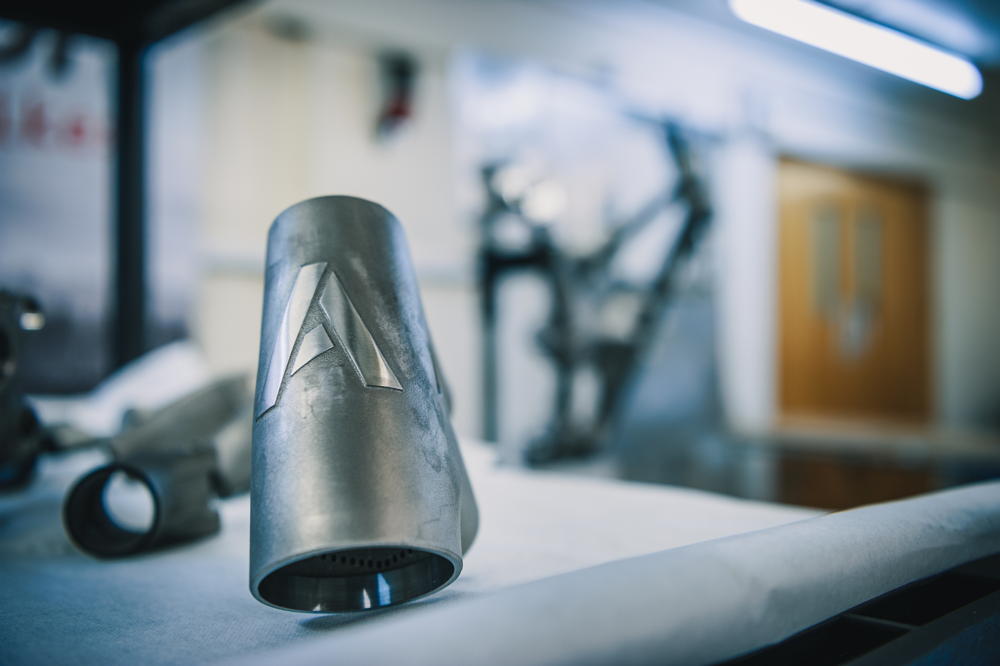
The Atherton name will sell bikes but the details impress too
Composite tubing makes sense for a mountain bike frame. It’s strong, light and allows for a modular construction method that gives a lot of design freedom. Joining these tubes together is the tricky part. Atherton Bikes work with Renishaw, experts in metal 3D printing technology, to create the lugs that join the tubes together. The lugs are printed using titanium powder that is melted by lasers, with each frame requiring 16 hours of machine time to print.
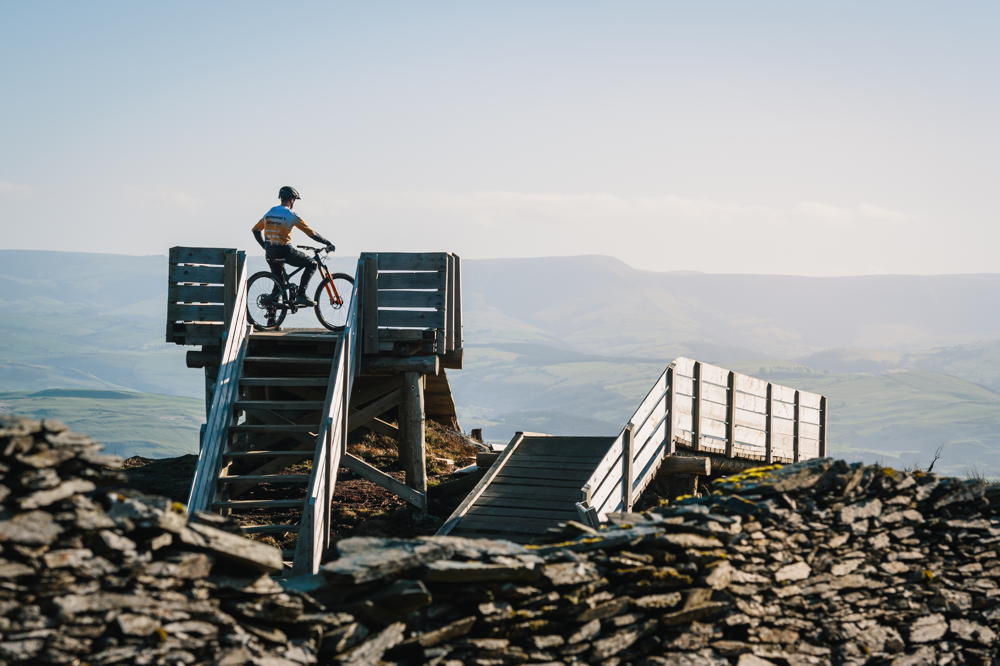
The top step is the Athertons’ natural home
3D printing gives a number of advantages over traditional casting or CNC machining. It allows parts to be made to very high tolerances with a level of detail — internally and externally — that no other manufacturing process can achieve.
The lugs use a double-lap shear joint into which the tubes are fitted and then bonded with a two-part adhesive. People get a bit twitchy about the idea of their frame being joined with adhesive, but this kind of bonding literally holds our world together. It’s a proven technology found on jet fighters and race cars, where low weight and high strength are critical.
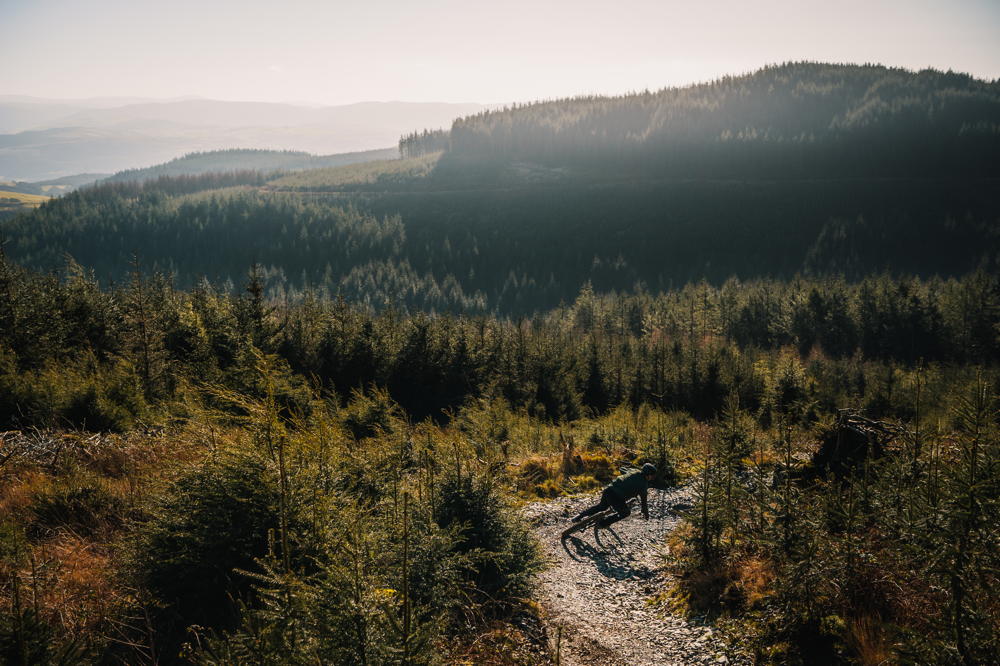
Dyfi Bike Park is the family firm’s own testing ground
When it came to designing the suspension, the team enlisted the help of Dave Weagle, a man who knows how to design a winning suspension platform. The DW6 suspension design that is used exclusively by Atherton Bikes is every bit as clever as you would expect and complements the thinking behind the frame perfectly. One of the main benefits is that the design architecture uses a set of fixed pivot points on the main frame, but a lot of adaptability and tuning potential back from that. The DW6 design makes it relatively simple to make changes to seatstay and chainstay lengths, leverage ratios and other elements, all independently of one another, while still retaining the desired pedalling and braking characteristics.
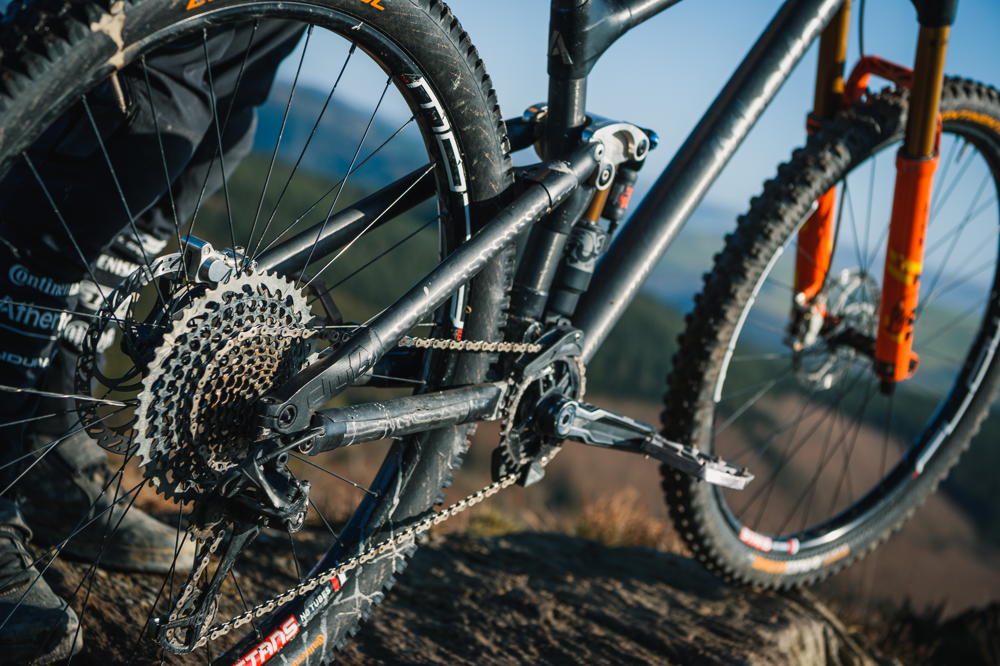
DW6 suspension is adjustbale for seat and chainstay length
This adaptability and speed of construction, thanks to the way the frame has been designed, is ideal for building the perfect race bike. Dan Brown, the Athertons’s manager, says that the quickest turnaround they’ve managed is four days. After finishing a World Cup race on a Sunday, Rachel decided she wanted to try a different back end on her bike for the race the following weekend. They designed the new parts on Monday, had them 3D printed by Wednesday, back to the factory on Thursday and by Friday the new back end was with the team. This super-short feedback loop is invaluable to a race team constantly looking for improvements — even if in the end Rachel preferred her original set-up.
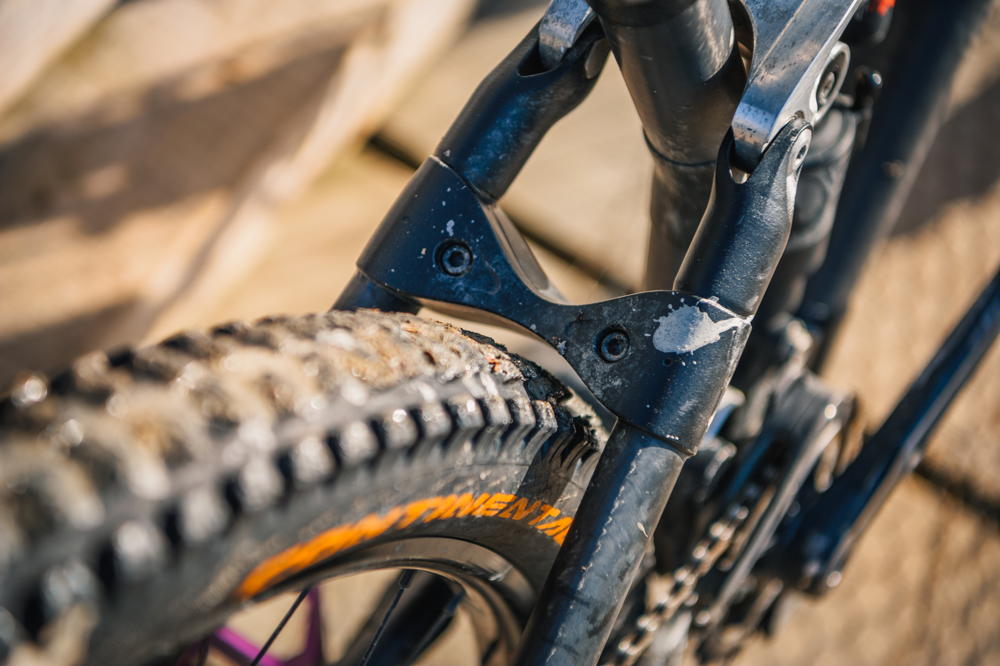
Testing feedback led to seatstay bridge
While this agile manufacturing works well for creating bespoke builds, Atherton Bikes maintains that it also works for large-scale production. Atherton Bikes may well be a start-up at present but it’s got an eye on the future and growth. Right now it is still testing systems and tackling all the usual problems a fledgling business faces — one of the most pressing problems being coming up with model names. With the bikes due to go live on the website imminently, a decision will have to be made soon, but for now the enduro mountain bike frame currently being assembled is simply called ‘the 150’.
Test facility
A day later, and 100 miles north of Monmouth, I’m riding shotgun in a lifted Land Rover Defender as it grunts and snarls its way up a Welsh forest track. Monster truck tyres splash through grey puddles and make light work of the mud, rocks and branches that cover the fire road. Dan Atherton is behind the wheel. Today we’re in the Athertons’ forest, to ride their trails on their bike — something members of the public will also be able to do soon. Dyfi Bike Park just outside Machynlleth is part playground, part proving ground and very much open for business.
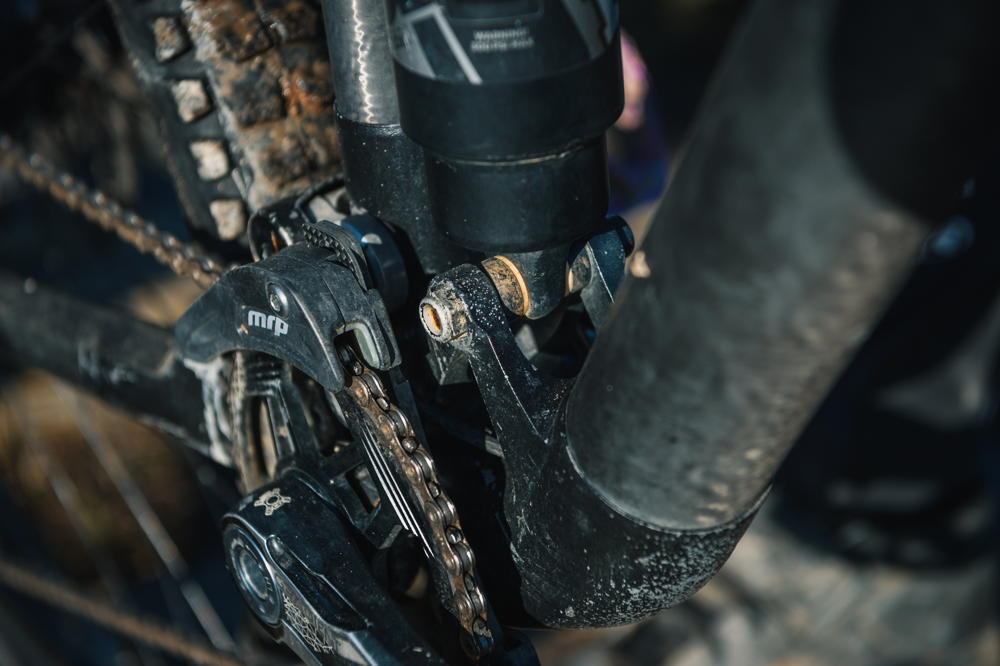
Evidence of hard use on moving parts
When the Athertons bought the forest in which the bike park is built, they also took on a timber yard. A good portion of Dan’s day is taken up with managing the growing, felling, transportation and sale of wood, and his phone buzzes constantly with questions of woodland logistics, staffing and machine repairs. While being a sponsored rider with a bike company and a forest full of trails might seem glamorous from the outside, there’s a lot of real graft being put in to make the many dreams happen.
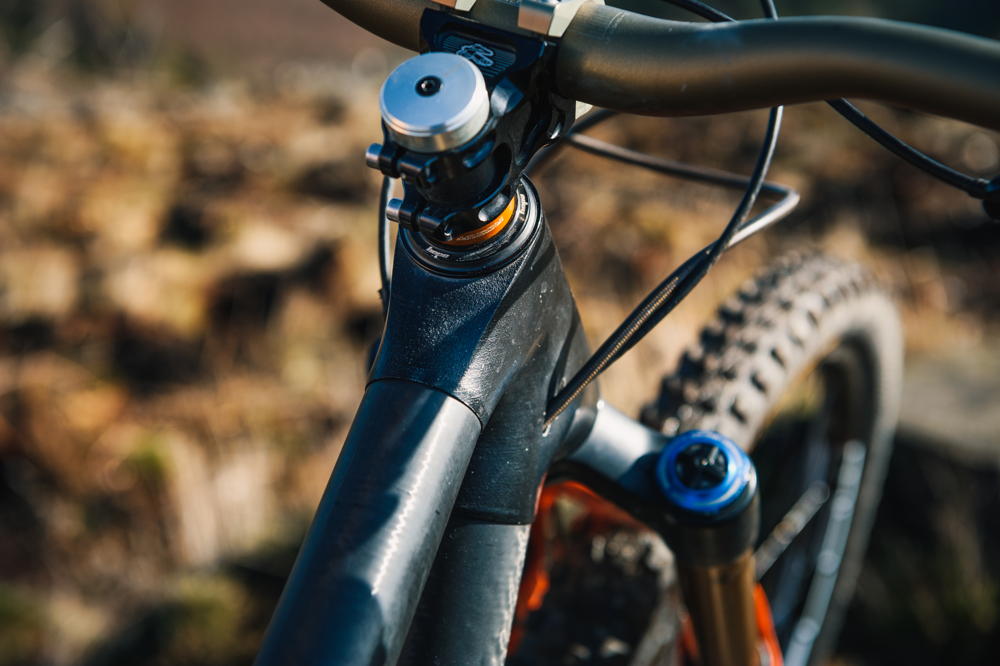
Black finish for test rigs but lugs and tubes stilll look distinctive
Atherton Racing is a well oiled machine with a long and successful history. Atherton Bikes and Dyfi Bike Park are still very much fledgling enterprises. Launching just one of these ventures would be a tough task, but launching both a bike company and a bike park at pretty much the same time — while also keeping the race team at the top of the pile — is a monumental undertaking. The Athertons’ manager, Dan Brown, agrees: “As with everything the Athertons do, it’s all or nothing.”
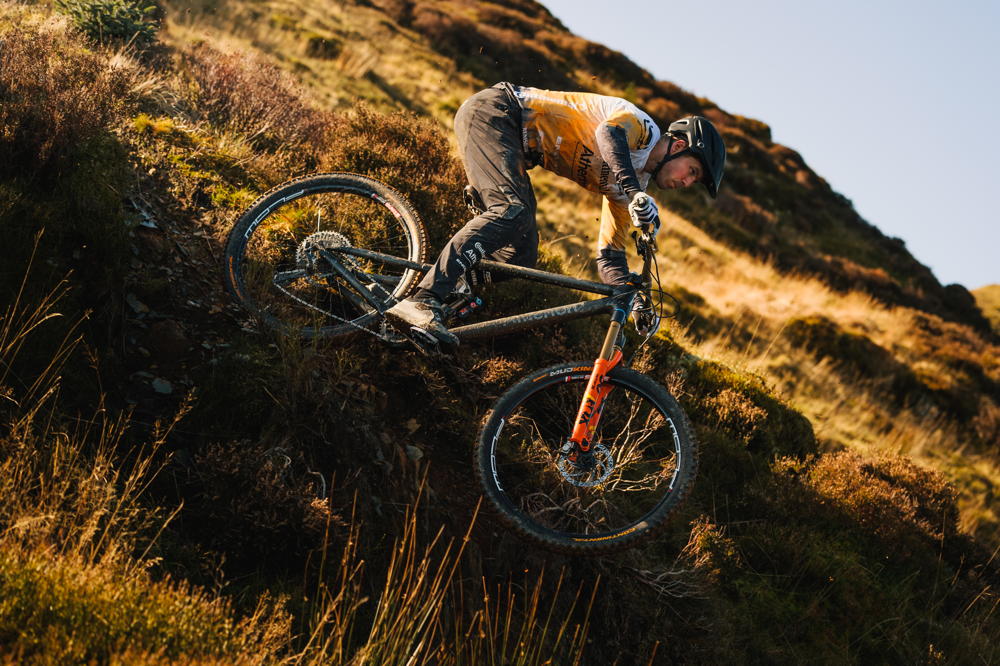
Leaning in is easy when the bike will bear the family name
While Gee and Rachel have been putting the downhill bike through its paces, the 150 is very much Dan’s bike. It comes from his experience as an enduro racer but also as an incredibly talented all-round rider. This is the bike he wished he had when he was racing enduro — a bike built to be fast and to take a beating.
Dan’s talents extend beyond just riding; he’s also a master trail builder. With a forest at his disposal, the skill to build great trails, and the ability to push a bike to its limits, he’s uniquely placed to provide feedback on the bikes.
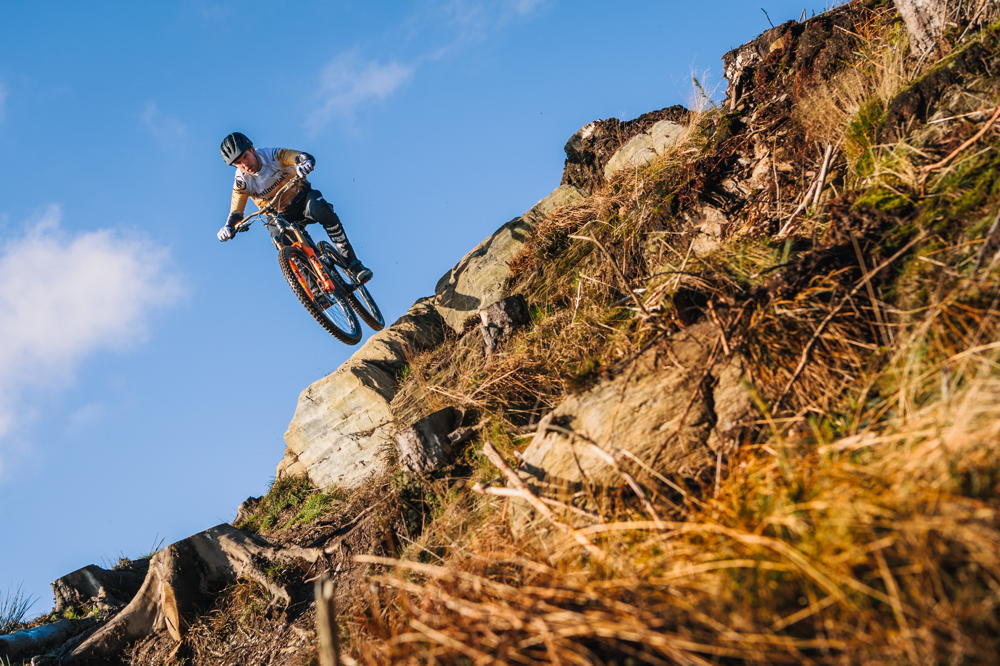
Welsh rocks: is there a better place to test prototype machines?
Feedback is one of the things that makes Atherton Bikes unique. Plenty of brands say their bikes are built with input from their sponsored athletes, but how much of that is lip service is hard to tell. Atherton Bikes is built on the fact you can have exactly the same downhill bike as Gee or Rachel, not just a bike with the same paint job. Equally, the 150 draws on Dan’s DH, enduro, 4X and bike park experience. Having trails that he knows intimately, can session time and time again and are conveniently closed midweek, makes Dyfi Bike Park the perfect testing ground. They aren’t messing about with the trails here either — a triple black diamond run is just one of the four trails currently open at Dyfi. The mixture of trails and features means that in the morning they can session jumps and turns, and in the afternoon concentrate on rough, rocky sections.
Air time
From the start ramp, you look down onto the clear hillside felled of trees. Beyond that stretch the rolling hills of mid Wales. It’s a rare opportunity to take in the great view; from here on in, the trail demands your full concentration. A set of decent sized drop-offs act as a qualifier before sending you into a series of large jumps. These are the kind of jumps that, when cleared by a decent rider, make you realise just how much air time is on offer. Dan goes skyward. And keeps going. And going. It’s a stark reminder that while feedback from general riders is important, feedback from great riders is invaluable.
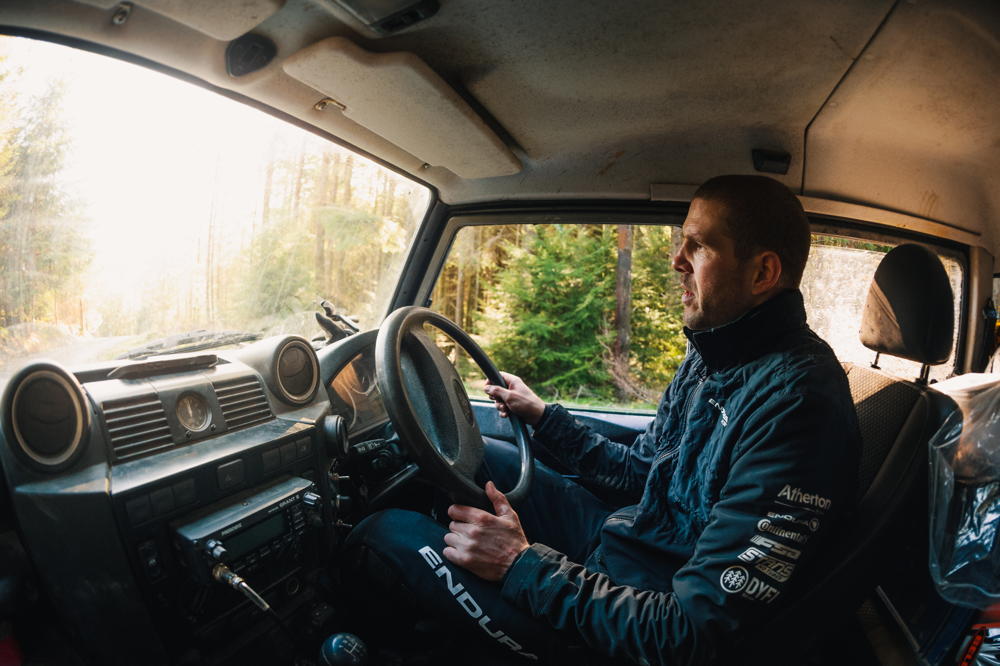
Dan continues the search for the perfect test trail
Back in the Land Rover is where a lot of the feedback occurs. Frame designer Rob will come up from Monmouth and ride with Dan, and on the crawl back up the hill they’ll chew over what they were feeling on the previous run. Emails, phone calls and WhatsApp messages all work, but none are as valuable as face-to-face conversations right after riding. From these casual conversations requirements can be drawn up and numbers and specifications can be generated. Changes can then be made and the process starts over again.
Real world
A good example of this was the rear stiffness of the 150. During initial testing, Dan felt the rear of the bike needed to be stiffer, as when he was pushing it into a series of turns in the bike park, things didn’t feel quite right. This was backed up when journalists, such as mbr’s own Mick Kirkman, were invited on a testing day and their feedback matched Dan’s.
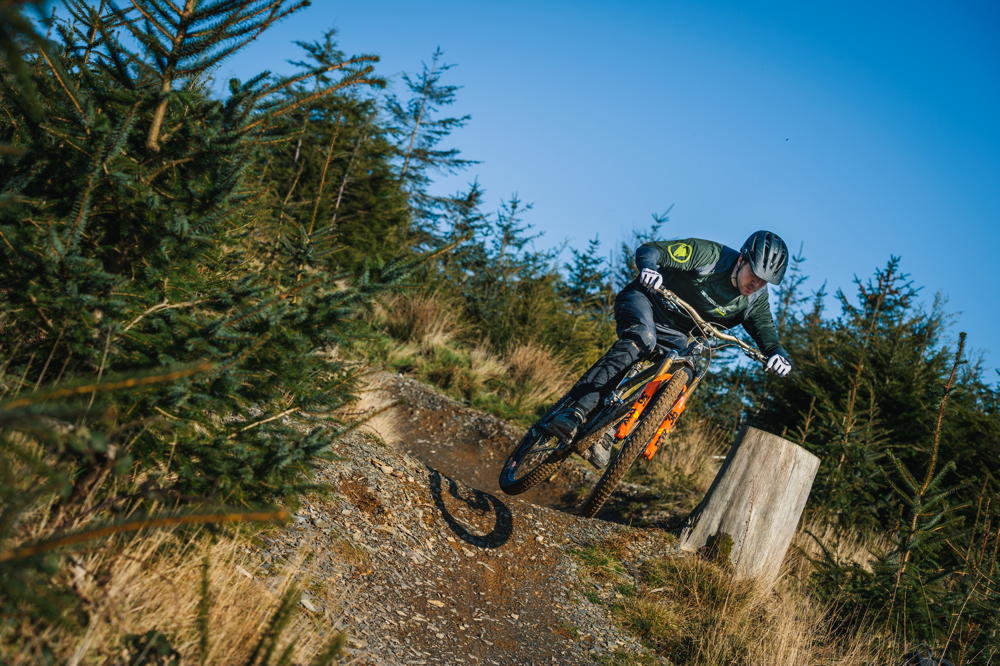
Feedback from the trails is invaluable for design tweaks
Using that feedback, a prototype brace was designed, 3D printed and bolted to the chainstays of Dan’s development frame. The brace actually proved to be too stiff, but with refinement and further testing, the right level of stiffness was introduced to the back end and a much neater chainstay brace was developed for the production bike.
Using racers for feedback isn’t always easy though. Over a cup of tea in the saw mill, Rachel explains the dilemma of being a racer and constantly striving for that change that will give you the edge. With the opportunity to make changes from race to race, there’s a temptation to keep on changing, when what you sometimes have to do is stick with what you’ve got and learn how to make it work. Rachel points out that that could well take a whole season, so change for the sake of it isn’t always useful. Nor is it useful in terms of making and selling bikes — at some point you have to settle on geometry and kinematics and start selling bikes — after all, that’s the reality of Atherton Bikes.
Not only is a bike park a great place to test products, it also provides the perfect opportunity to get a view outside the race scene. Sat at the bottom of the hill, Dan can see what bikes people are riding, how they set their bikes up, what works and what breaks. This is all valuable information that can be used to inform decisions, both for the development of the bike park but also for Atherton Bikes.
Every mountain biker dreams of being paid to ride their own bike, of having their own bike brand and a piece of hillside to dig trails on. It’s reassuring to find out that even pro athletes have the same dreams as regular riders.
The Atherton family have worked hard to make those dreams a reality, but they have also given the rest of us the chance to share in those dreams, if not the podiums.