Busted bearing need not sound the death rattle for e-bike motors
“Sometimes we open one up and water will run out literally all over the floor. Then it’s a race to dry it out inside before the fresh oxygen turns the steel parts to rust, you can actually see it happening before your eyes.” That’s Peter Collard, a man who started an e-bike motor repair business from a log cabin in his garden four years ago, but now runs an international business fixing out-of-warranty motors.
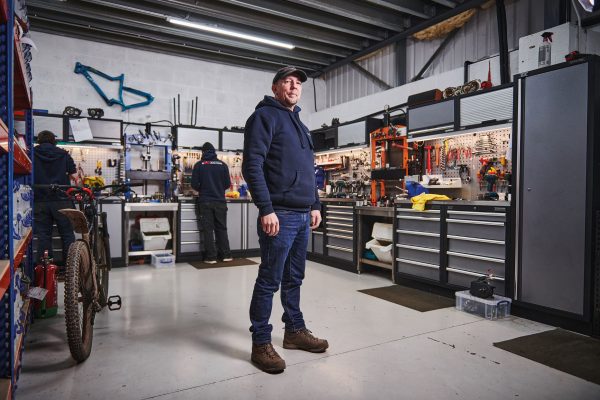
Peter Collard is on a mission to repair water-damaged e-bike motors
He proudly shows us his wall of horrors, motors with snapped axles, broken teeth, rusted components seized hard, and wiring that’s carried water right up into the motors circuit board. “People will swear blind their bike’s not been near a pressure washer, then you open it up and it looks like this,” Peter says, holding out the green and orange-brown carcass of a Brose T. “It only takes one drop of water to get through the bearings dust seals and eventually it’ll be game over for the motor.”
That’s where the eBike Motor Centre comes in. The idea is simple, even if the details really aren’t at all. All the while an e-bike is in warranty the bike shop or dealer will replace a dead or dying motor free of charge, usually by ripping it out and replacing it with an entire new unit. Not great for the planet, but not so harmful for your wallet. The minute that warranty is up, the cost is going to be down to you.
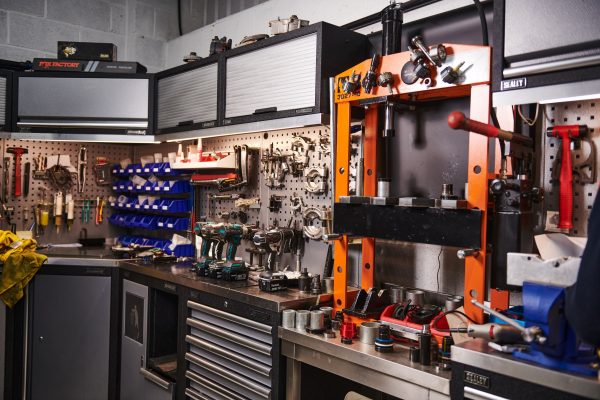
The Ebike Motor Centre was born in a shed but has evolved into a fully-equipped workshop facility
Peter and his team have spent the past four years learning how to source, fabricate and replace almost every part of a motor, outsourcing the electronics to a local firm, and returning it to the customer in good working order. Those that can’t be fixed are replaced with used motors of similar mileage and condition.
“People are so relieved we’re doing this, because suddenly all the weight of fixing a motor is lifted off their shoulders and they don’t have to pay up to £1,200 for a new one” Peter says. “It was easy for me to repair mine when it started in 2018, I had all the equipment and I’m a mechanical engineer, but others can’t so I wanted to help them.”
Like so many great mountain bike brands, eBike Motor Centre was born in a shed. A posh one, but an outbuilding nonetheless. While tinkering with his bike in his garden log cabin, Peter figured out he needed a new bearing. A simple repair for any half decent mechanic, but when he found it was bespoke to Bosch and couldn’t be purchased aftermarket he decided to make his own.
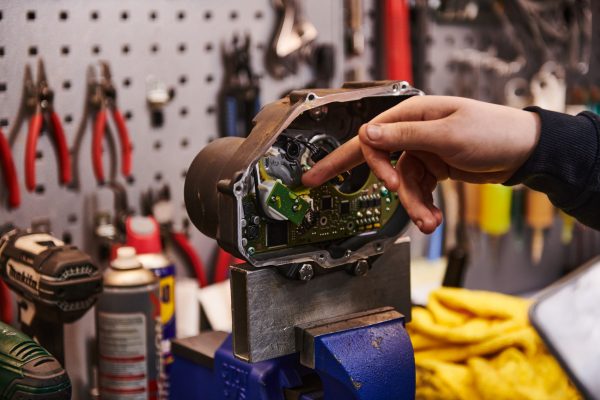
Peter and his team have spent the past four years learning how to source, fabricate and replace almost every part of a motor
“But you can’t just buy one bespoke bearing though, the minimum order is a thousand,” he says. “After fixing mine I had 999 bearings needing a home, so I stuck them on eBay.” Then people wanted the left hand bearing too, and any other parts he could find, and the business snowballed from there. Now the eBike Motor Centre’s outgrown its industrial unit in the New Forest.
Self starter
If this sounds like a business all the motor brands would want to help out and support, you’d be wrong. The most incredible part to Peter’s story is he’s figured everything out for himself, from the size of bearings needed to the software it’s running.
“Our biggest problem is we struggle to get any help with anything,” Peter says. “We were very lucky with Bosch, within the first six months they were knocking on the door and asking what we were doing. They’ve supported us and that was gobsmacking because they’ve been the only major brand that has.
“Although they use the Yamaha motor, Giant in particular is a very closed shop, we can fix them mechanically but we can’t do anything with the electronics,” he says. “Any other Yamaha we can put another circuit board in, that’s £200 and away you go.” The alternative for a customer is to send the bike to Giant, who’ll usually replace the entire motor for £900-£1200.
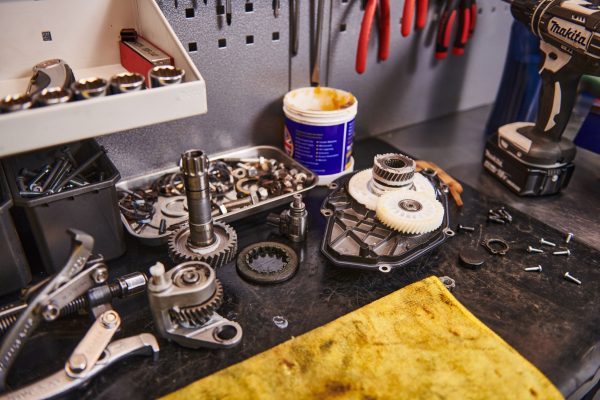
An e-bike motor getting a second life
It’s the software that proves the stumbling block to most repairs, Peter tells us, and with the exception of Bosch all the brands have been guarded with their software and won’t release it to third parties like the eBike Motor Centre. The fear is that motor brands will continue to exclude them and might even make it harder to repair the components without the manufacturer’s approval.
“That’s another of our big problems, just how popular we’ve been,” Peter says. “We’re supplying people all round the world, we have 24 partners globally and growing and every month we add another country. They come to us for the bearings and the motor parts, it’s growing exponentially and we’re expanding faster than we can finance.”
If that sounds like a nice problem to have, the implications for riders are problematic too. With 60,000 e-bikes sold in the UK every year, and a two-year warranty on most motors, the scale of support required is huge.
“This problem’s getting worse too, as the motors are getting smaller and lighter the parts and bearings are getting smaller and less durable,” he says. If seals are used, often they aren’t adequate to keep water out, he says, while the constant desire for more power and range precludes the use of proper waterproofing.
“I don’t know a single person who wouldn’t swap a few miles less range for an increased motor life,” Peter says. “But when you’re buying an e-bike you compare the stats and it’s the more powerful motors and those with the bigger range that will sell.”
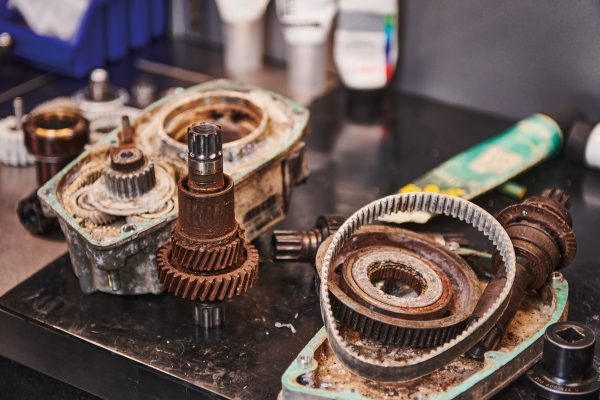
“It only takes one drop of water to get through the bearings dust seals and eventually it’ll be game over for the motor”
The eBike Motor Centre solution, at least for Brose motors that power Specialized Turbo Levos and Kenevos, is a £200 upgrade package that includes uprated heavy duty sprag clutch bearings, extra seals, exotic grease, and electrical plug treatment to stop water seeping up the wiring. It can be performed on a motor in good working order, or one in need of repair and of course this is great preventative maintenance.
“This was not the business I planned to start,” he says. “But I’ve really enjoyed helping people, giving people who would otherwise have to have had a new motor a different option.” Peter wants more brands to support and rubber stamp the essential work he’s carrying out, for the good of the planet to keep broken motors out of landfill, and to help riders with bikes out of warranty. Only then, perhaps, can e-bike riders allow him to retire.
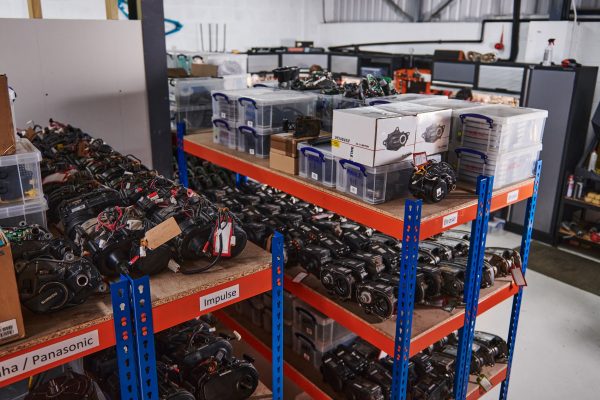
Peter wants more brands to support the essential work he’s carrying out to keep broken motors out of landfill